Our experimental work is often integrated with analytical or advanced numerical analysis which enables us to develop innovative solutions for our partners.
The Marine Structures Laboratory holds ISO 9001 certification and is operated jointly by SINTEF Ocean and the Norwegian University of Science and Technology, Department of Marine Structures.
Our test procedures are aligned with API 17J, API17B, Cigrè TB623, and Cigrè TB862.
Full-scale fatigue testing
Since 1997, SINTEF Ocean has designed and constructed two test rigs specifically for conducting full-scale tests on flexible risers, loading hoses, umbilicals, and power cables. The purpose of the full-scale fatigue testing is to demonstrate or qualify that the tested samples have sufficient service life when they are exposed to recurrent operational conditions.
These rigs allow combined axial tension and bending loads derived from global dynamic response analysis. Pressure and temperature load can also be applied to flexible risers and loading hoses during the fatigue testing according to their operating conditions. Bend stiffeners or bend formers are often mounted together with the test sample to replicate the actual installation.
Various methods are adopted to enhance the accuracy and reliability of the data acquired. These methods include the utilization of radiography and gamma-ray techniques, acoustic emission monitoring, acceleration measurements, strain gauge assessments of tensile armor wires, and digital image capturing (DIC) for curvature measurements along the bend stiffener region. Continuous monitoring of electrical resistance of both screen layer and conductor phases are provided in close collaboration with SINTEF Energy. These techniques have become integral components of our standard full-scale testing of marine slender structures.
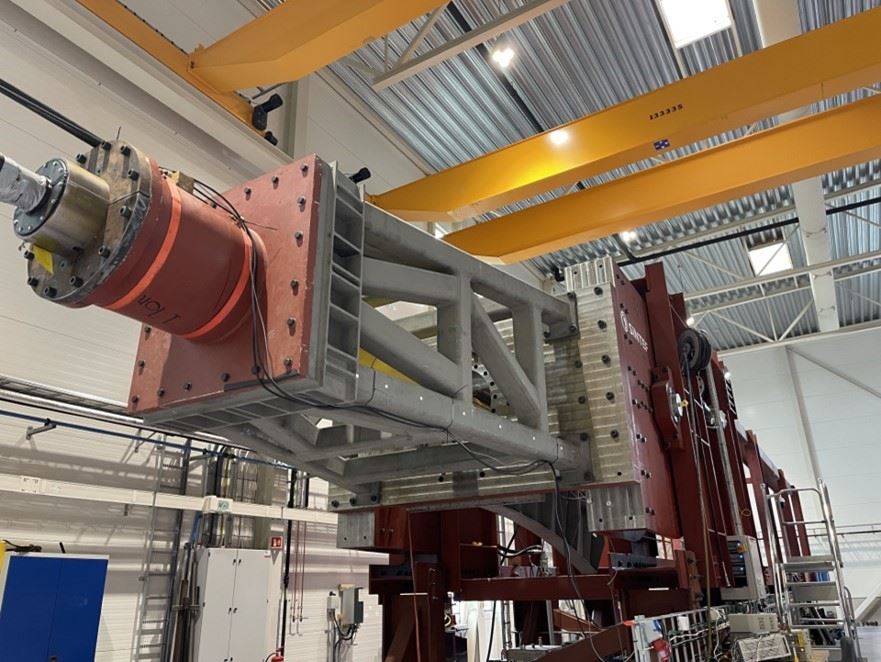
Full-scale compression-bending testing
In 2014 SINTEF Ocean designed and built a full-scale rig to test power cables and umbilicals subjected to cyclic and combined compression and bending loads. The purpose of the full-scale compression-bending testing is to replicate operational conditions which may trigger lateral armour-buckling in a cable or umbilical exposed to combined axial compression and cyclic bending.
Special methods are utilized to achieve constant curvature along the length of the test specimen at a given point in time. This will reduce the test specimen length required. Repeated bending cycling is applied in an automatic manner by keeping the compression constant during each bending cycle. In order to avoid global buckling effects during testing, the test specimen is loaded in such a manner as to ensure that the total effective wall tension/compression close to zero, while the local components are in compression.
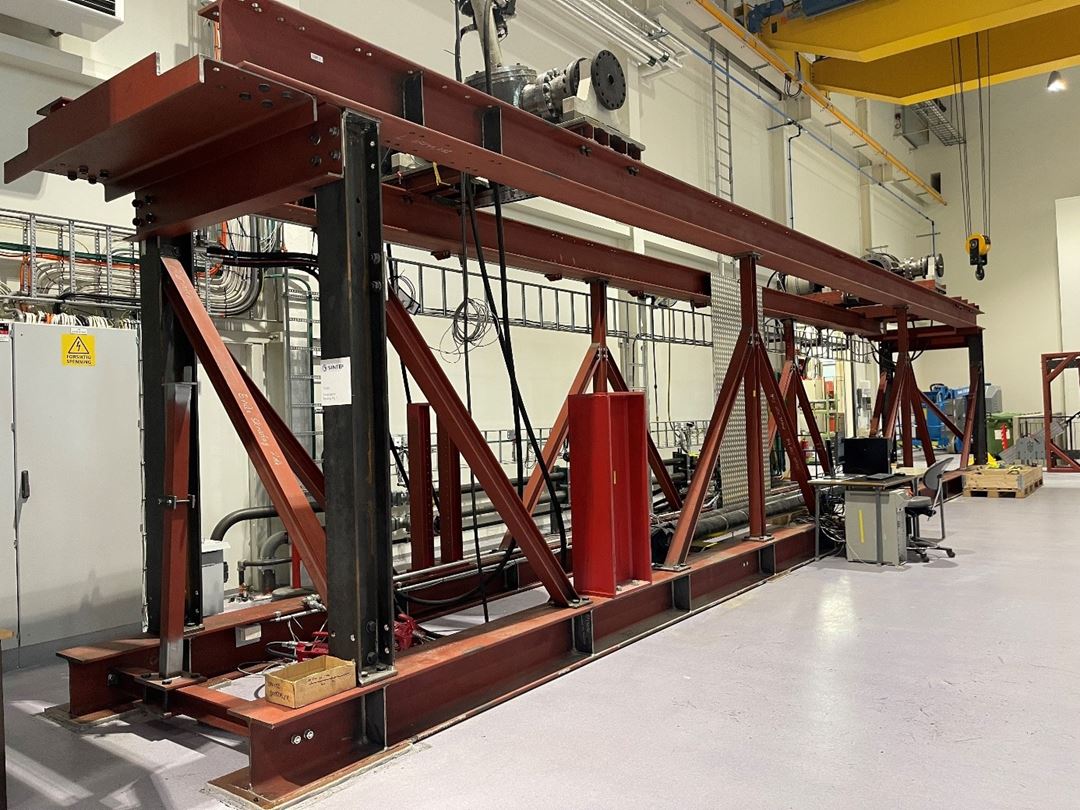
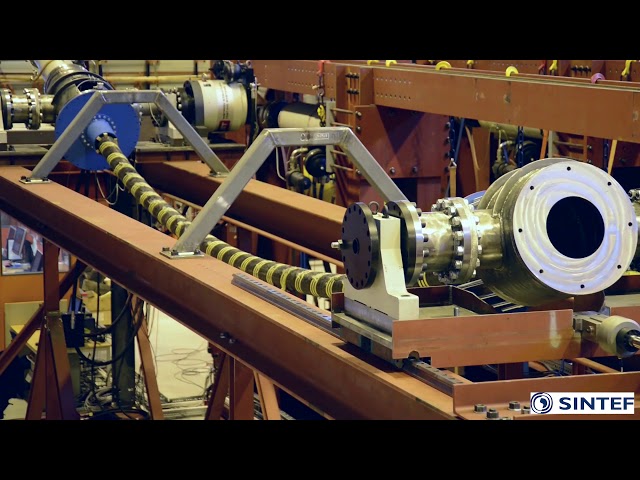
In-situ bending property testing
Several test rigs are available for bending property testing of flexible risers, umbilicals, and power cables. The testing can be operated either in three-point-bending or four-point-bending configurations. The purpose of full-scale bending property testing is to construct the actual relation of bending moment and curvature of the test samples. The results from the testing are crucial in refining the numerical models in removing the uncertainties in capacity estimation and enhancing lifetime predictions.
Our novel three-point-bending test rig is integrated with the full-scale fatigue test rigs. This integration allows axial tension to be applied during bending property testing, making it the most reliable method for determining the intrinsic bending properties of test samples, particularly for power cables.
Torsion testing
A conceptual torsion test rig is built for better understanding of torsional behaviour of marine slender structures. A full-scale torsion test rig will be built based on the outcome of the conceptual torsion test rig. The results will also be essential in calibrating a numerical tool developed by SINTEF Ocean for calculating the torsional capacity of the marine slender structures.
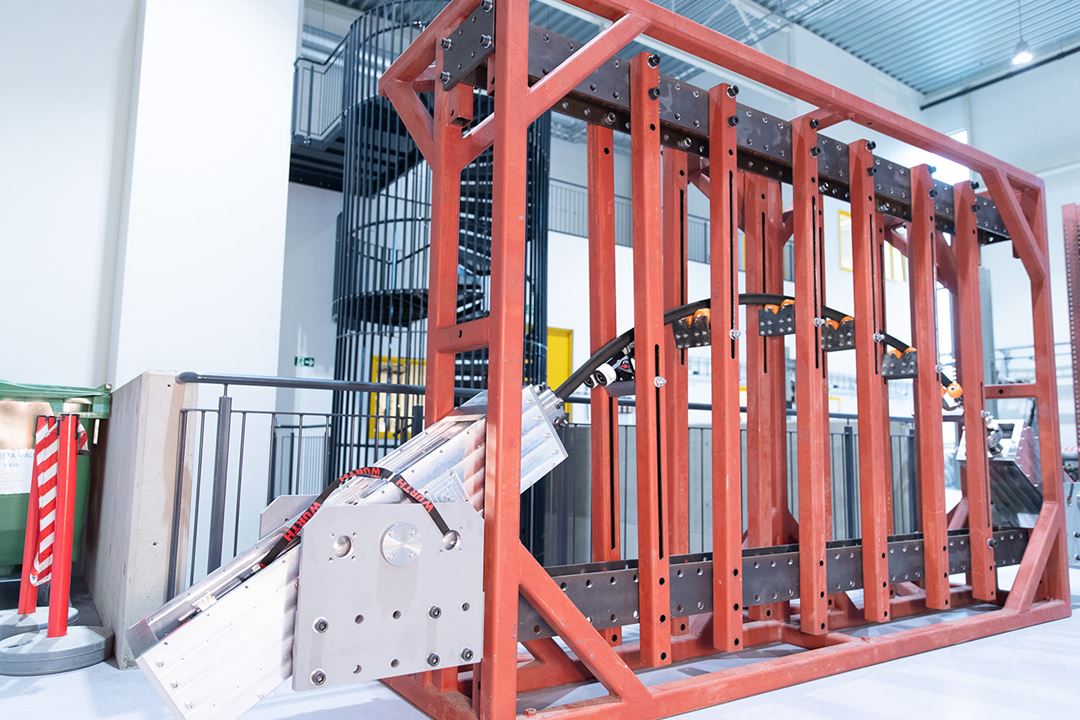
Component fatigue testing
Two test rigs are developed for fatigue testing of stranded conductors, which include power phases from typical three-phase power cables. The purpose of the component fatigue testing is to determine fatigue properties of the stranded conductors under combined bending and axial tension. The outputs from the testing will enhance our confidence in fatigue calculation methodologies. Traditionally, lifetime predictions for stranded conductors rely on fatigue data obtained from single wire fatigue testing. However, the fatigue properties of these conductors may significantly differ from the performance observed in single wire fatigue testing.
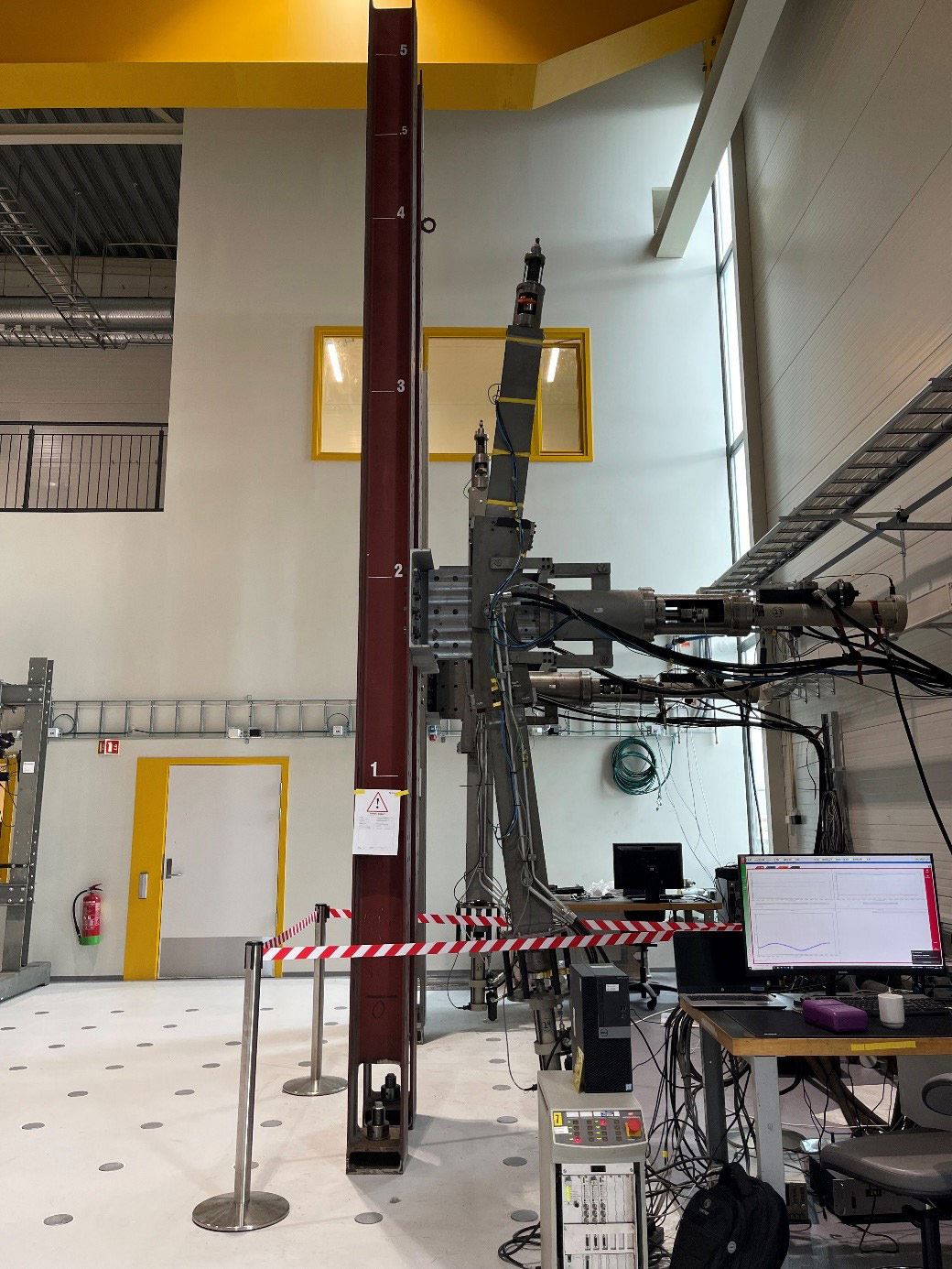
Material testing
A number of test rigs are available for material testing. Various of material testing can be performed in these rigs, which includes tensile property testing, friction coefficient testing, and single-wire fatigue testing etc. The purpose of the material testing is to create comprehensive databases of material properties. These databases will serve as a foundation for precise predictions regarding the physical properties of the end products, facilitated by SINTEF Ocean's advanced numerical modelling techniques.
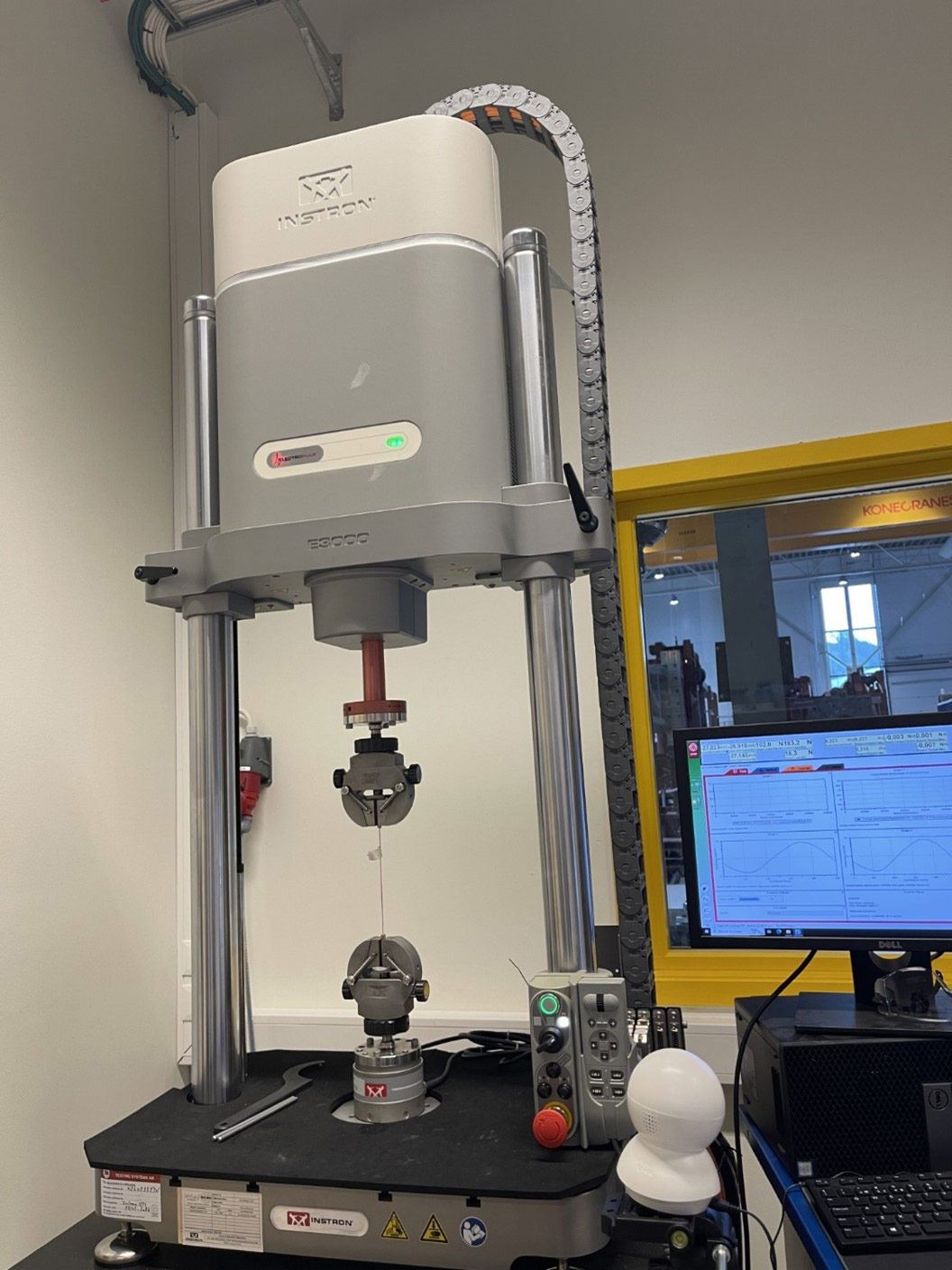
Testing rigs on the strong floor
The marine structures laboratory is equipped with a strong floor with an area of 12 000 mm x 7 800 mm. The strong floor is fit with built-in fixation points at an interval of 600 mm in both the length and width directions which makes it efficient to build special test rigs upon specific requests. Maximum vertical point load at the fixation point is 1 MN and maximum horizontal point load in either direction is 2 MN. Maximum bending moment is 1MNm about the horizontal axis.

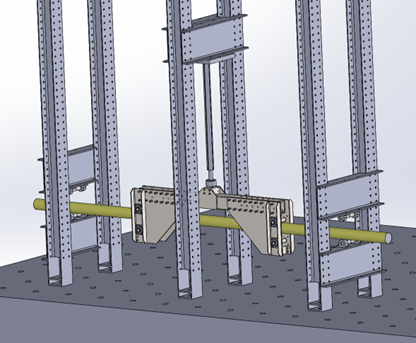
General structure testing
A brand-new universal test rig is available to carry out general structure testing. The test rig is integrated with a universal work bench which enables efficient testing using user-defined setups.
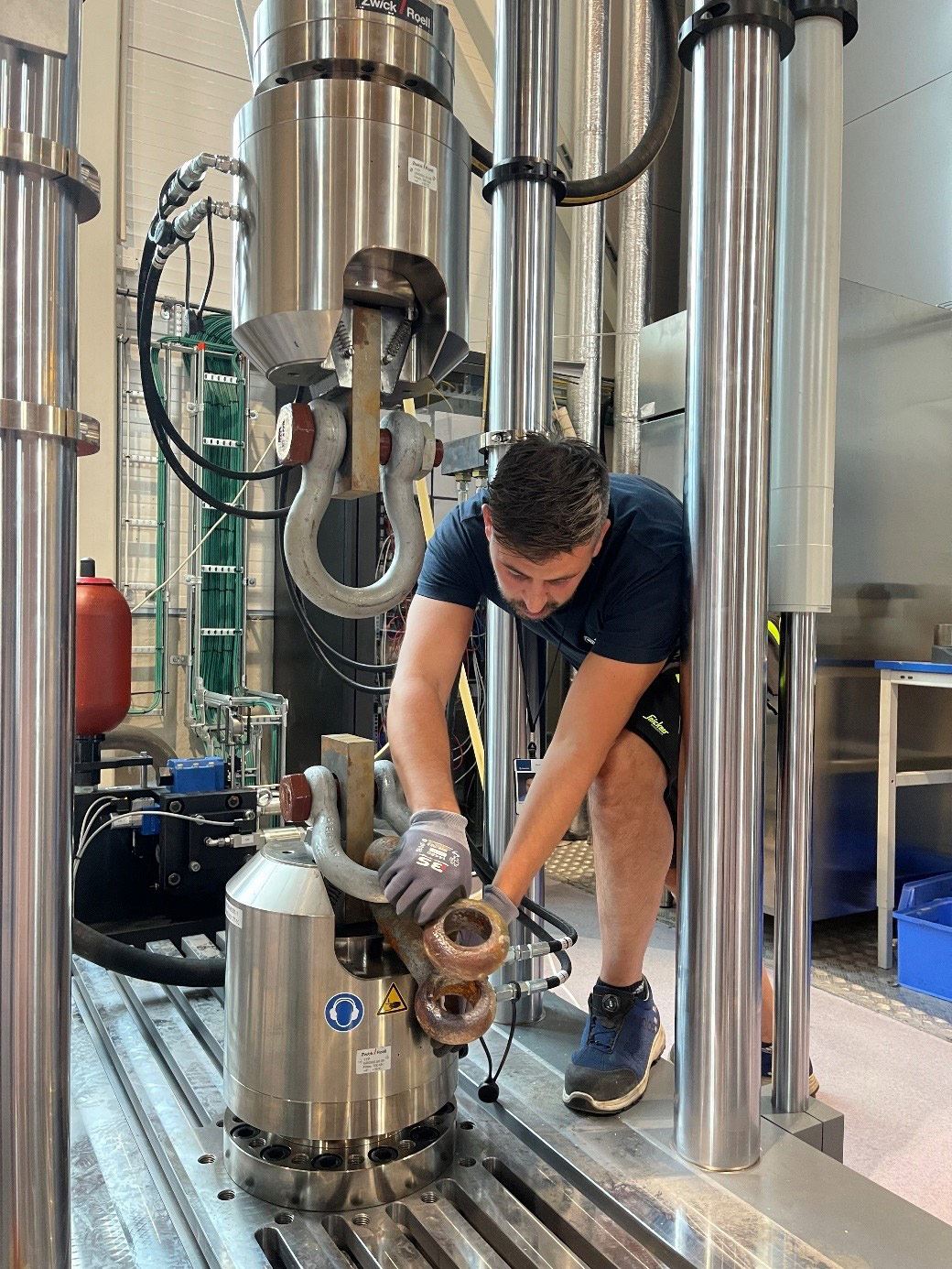
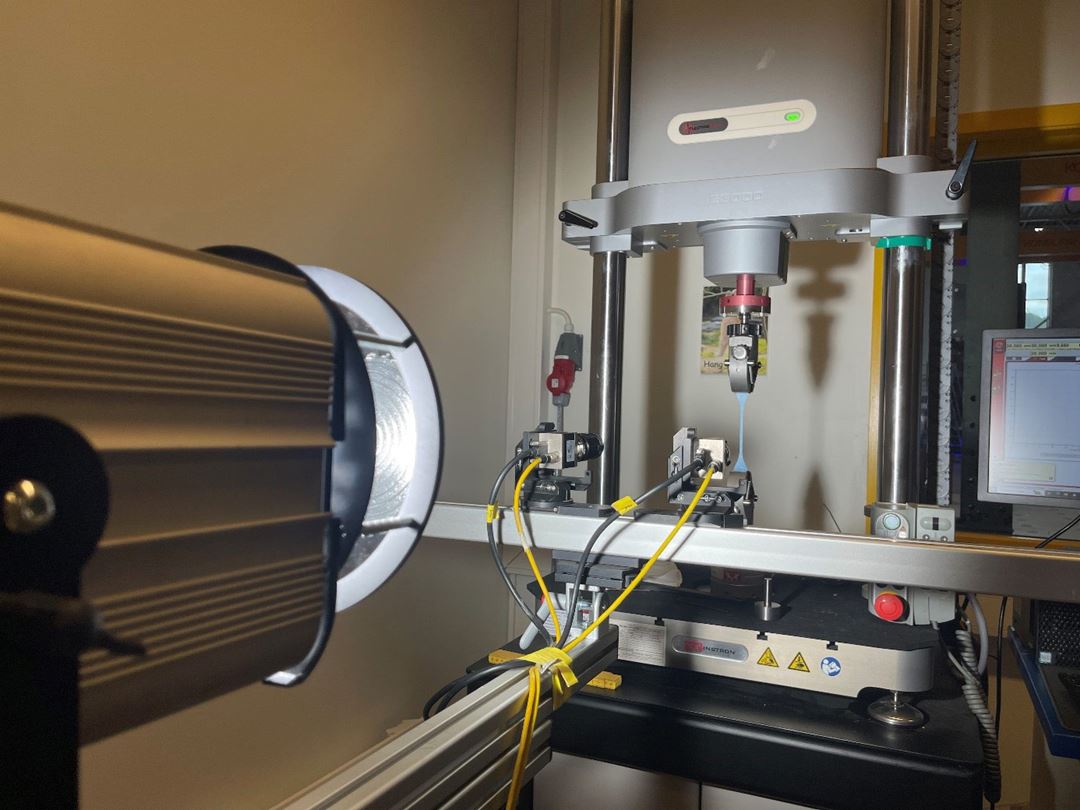