General information
Material innovation is key to enabling the products and technologies that will build a better society. Advanced mechanical characterization is a vital part of this innovation.
We specialize in the mechanical testing of:
- Thermoplastics ("plastics”)
- Thermosets (cross-linked)
- Elastomers and rubbers (cross-linked)
- Advanced polymer matrix composites (with short and continuous fibres)
This lab complements the other four main labs of the Polymer and Composite Materials research group, the polymer chemistry lab, the material characterization lab, the processing lab and the ageing lab
We have additional experience in the mechanical characterization of:
- Multi-material and sandwich core laminates
- Reinforced and coated fabrics
- Wood and other bio-composites
- Ductile metals exhibiting plastic behaviour
- Adhesion between parts (e.g. adhesive bonding and weld lines)
- Interfacial friction and wear properties
Standardized testing generally follows ASTM and ISO test methods. We can however accommodate most any other method and guideline necessitated by a given industry and application. We also excel at testing new and challenging materials and applications thanks to competences that set us apart:
- Relating material behaviour to processing (e.g. injection moulding, filament winding and additive manufacturing), as well as ageing and recycling
- Developing and implementing novel test methods, fixtures and equipment
- Supporting experiments with advanced finite element modelling (FEM) to validate test results and calibrate advanced material models used in design, certification and lifetime prediction
- Providing comprehensive services including specimen preparation (processing and machining), pre-test conditioning and ageing, and fractography
Finally, we operate as part of a large ecosystem of lab facilities at SINTEF and its partners that can support most any industrial and R&D application from deep sea to outer space.
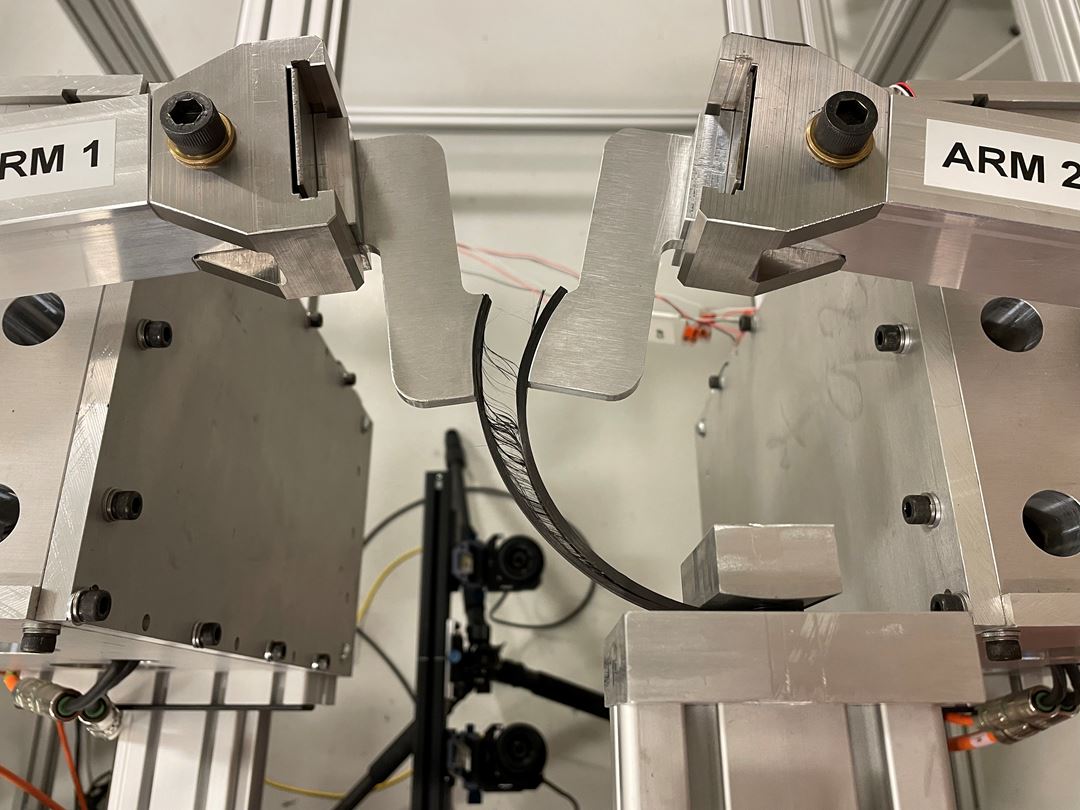
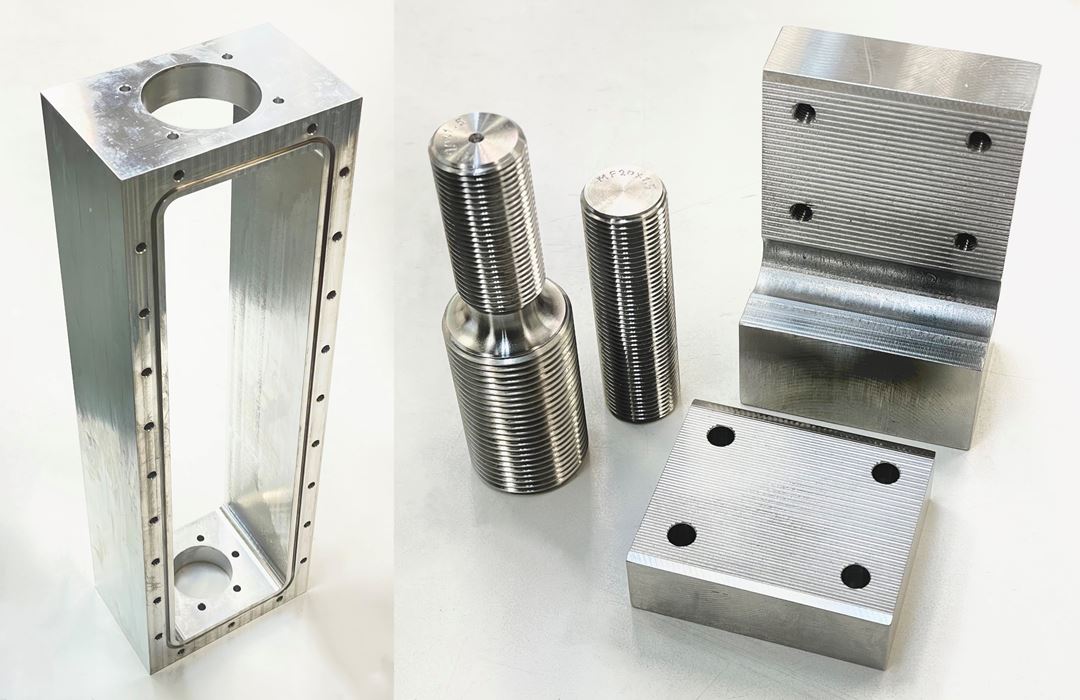
Equipment and capabilities
Quasi-static testing
- The “workhorse” in this lab is a Zwick/Roell Z250 universal test machine with a load capacity of 250 kN. This load frame can be configured with multiple load cells (down to a few Newtons) to perform a wide variety of high-accuracy, standard tests (e.g. tension, compression, flexure, shear and friction) as well as more complex, programmable loading schemes.
- Tests can be performed at temperatures ranging from -80 to +250 °C using a temperature chamber.
- Strains can be measured with a long stroke extensometer (ca. 800 mm of travel), a clip-on extensometer, strain gauges or with a contactless digital image correlation (DIC) system (see below). DIC further allows for volumetric strains to be measured. Test specimens can also be instrumented with acoustic emission sensors.
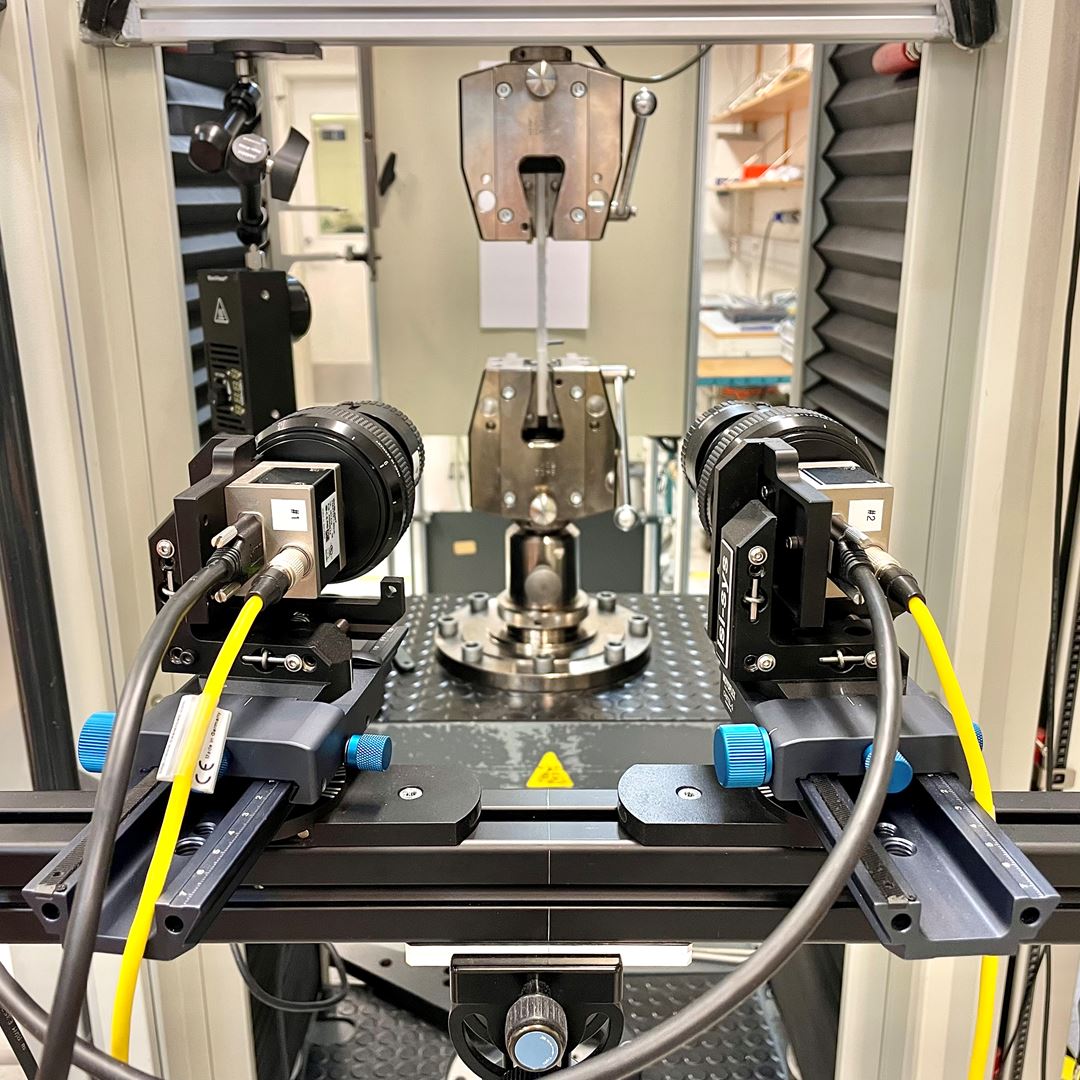
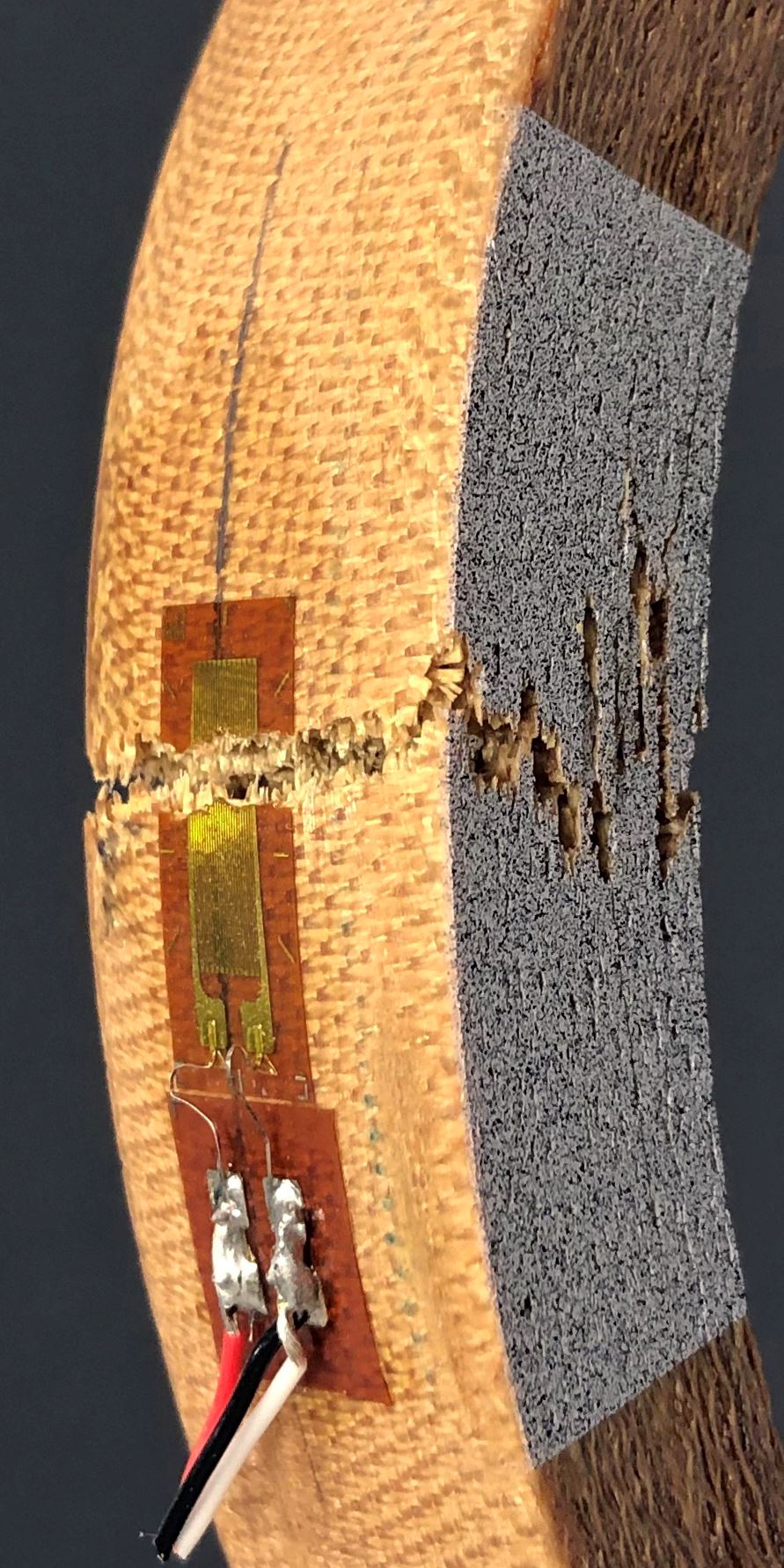
Cyclic and fatigue testing
- The lab has two Instron hydraulic fatigue testing machines with load capacities of 100-kN and 25-kN. Both are capable of also running certain quasi-static tests.
- Various fixtures and grips can be installed to perform fatigue tests in tension, compression, flexure and shear.
- Tests can be performed in a water chamber, including DIC strain monitoring and temperature control.
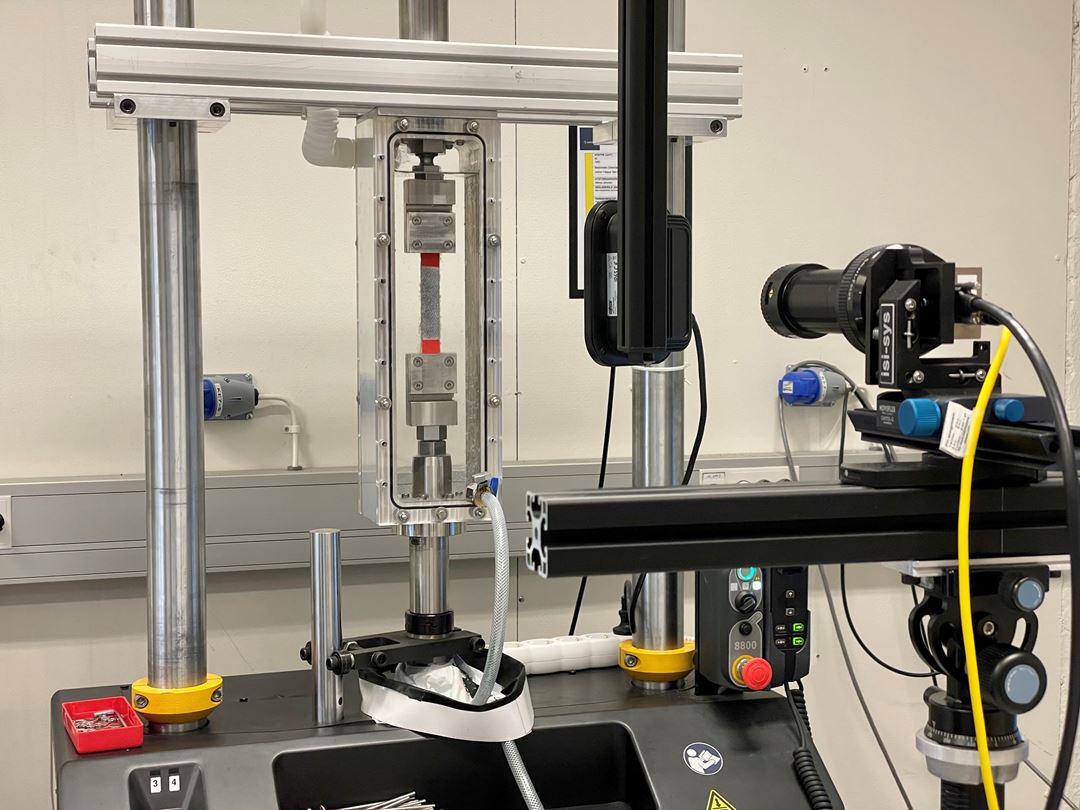
Delamination testing
- We have developed a novel, moment-based delamination testing machine capable of testing polymer composites and multi-material laminates (and components) in fracture modes I, II and III, as well as any set ratio of modes I and II (mode mixity).
- We can additionally obtain traction-separation (or cohesive) laws for finite element modelling using the J-integral approach in concert with our advanced 3D DIC system (see below).
- Uniquely, this test setup enables the testing of curved specimens and components (e.g. filament wound laminates) in pure mode I.

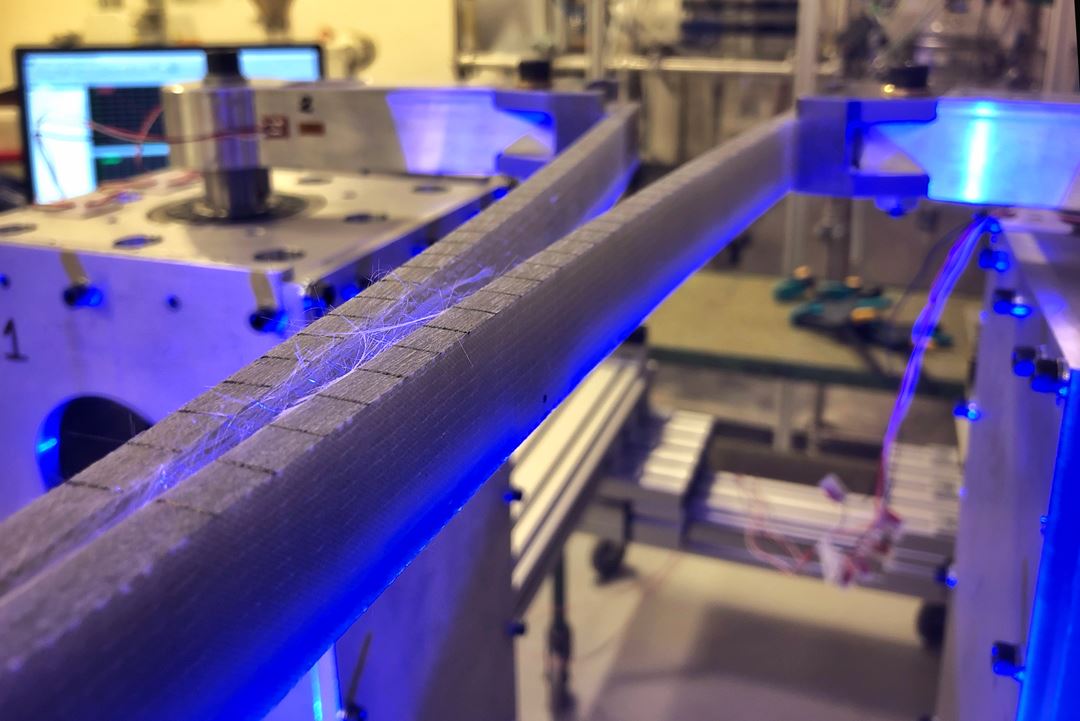
Digital Image Correlation (DIC)
- We use an advanced DIC system for position (target tracking) and strain measurements in both 2D and 3D (mono and stereo vision, respectively) depending on the application. This optical system is mobile and modular and can be adapted to work with the aforementioned test machines in both static and dynamic loading. Several stereo systems can be used together in a single test to simultaneously monitor separate surfaces and fields of view, and even stitched surfaces for cylindrical specimens.
- The system has a field-of-view ranging from 15 mm to several meters. It is developed by Correlated Solutions Inc., and supplied by isi-sys GmbH.
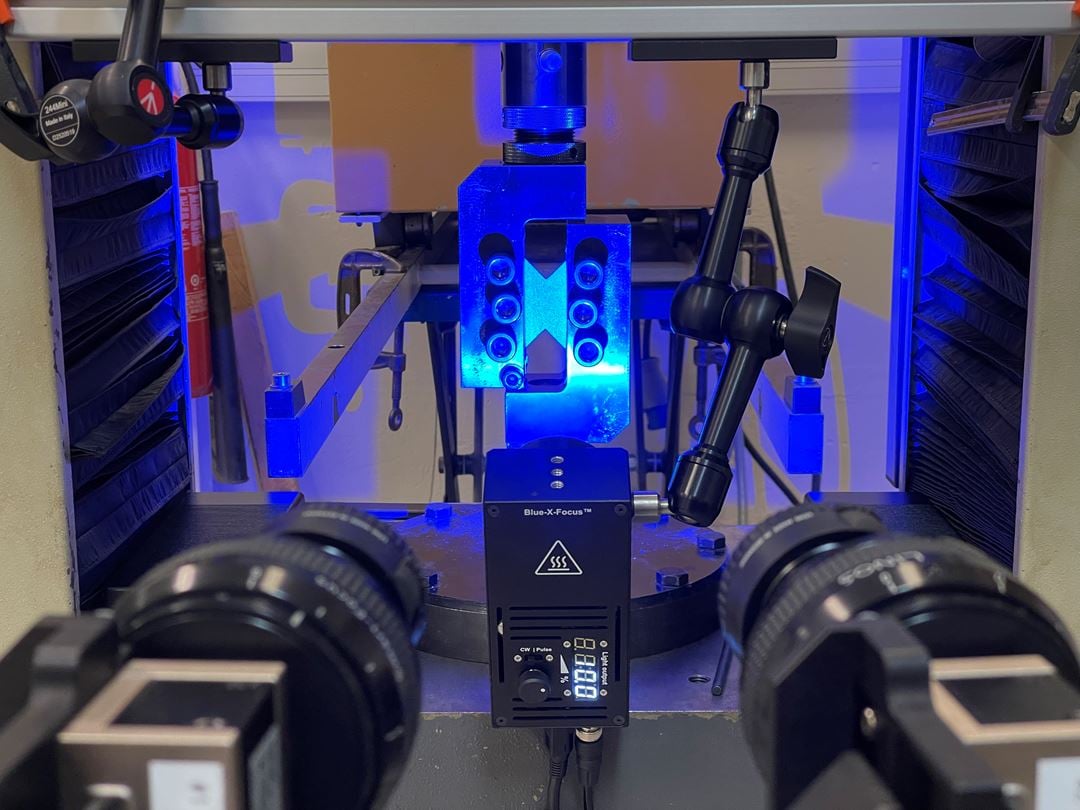
Impact testing
- The lab has an Imatek, falling weight impact test machine that is mainly used to perform Charpy and Izod impact tests. It is instrumented with a piezoelectric sensor to record the force during impact and accommodates a wide range of striker tips and small fixtures to hold specimens and products.
- The maximum velocity of the striker is approximately 4.5 m/s (a higher velocity can be achieved with the use of an elastic cord). The striker mass can be varied from 3.5 to 40 kg.
- Tests can be performed at temperatures ranging from -80 °C to +200 °C.
Creep testing
- The lab has a test rig that can accommodate up to 24 specimens for long-term creep testing under a constant tensile load. A maximum load of 500 N can be individually applied to each specimen.
- Tests can be performed at ambient temperature in both wet and dry conditions, and at elevated temperature up to 80 °C while immersed in a heated water bath.
Other equipment
- Instrument for measuring hardness (durometer) of hard and soft polymer materials (Shore A, Shore D, micro Shore A, IRHD)
- Rigs for measuring compression set of elastomers/rubbers
- Instrument for dynamic mechanical-thermal analysis (DMTA, DMA), see the material characterization lab
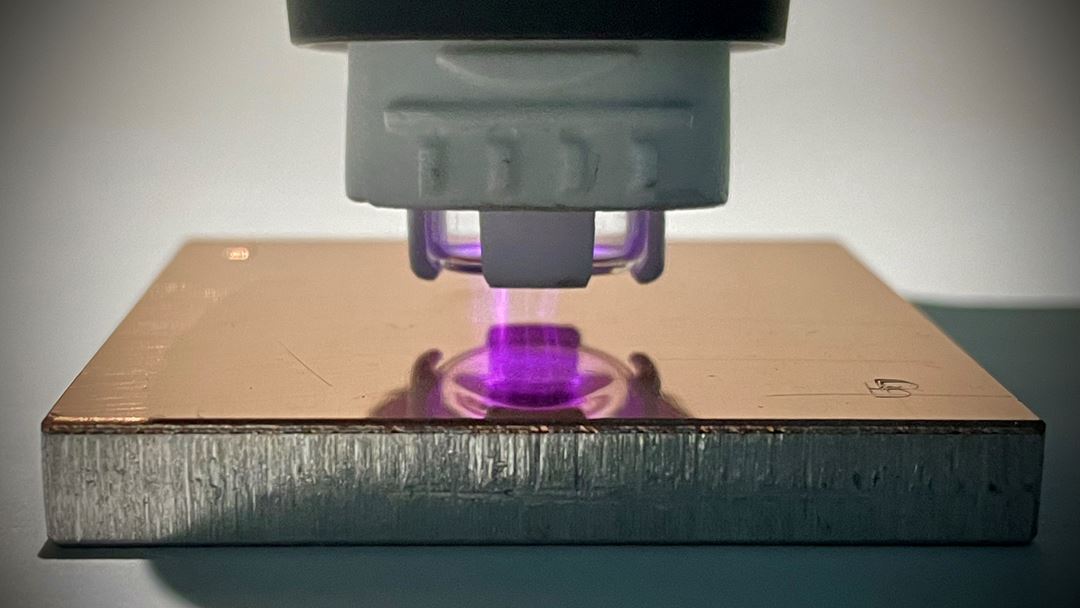
Relevant test standards
Listed here are standard test methods that we more commonly use and are familiar with, but it is by no means exclusive.
Thermoplastics and thermosets (incl. reinforced materials)
Tension: ISO 527 / ASTM D638
Compression: ISO 604 / ASTM D695
Flexural (bending): ISO 178 / ASTM D790
Shear: ASTM D5379, ASTM D7078
Impact: ISO 179 (Charpy), ISO 180 (Izod), ISO 6603 (puncture impact)
Fracture toughness: ISO 13586, ISO 17281
Fatigue: ASTM D7791
Elastomers and rubbers
Tension: ISO 37
Compression: ISO 7743
Compression stress relaxation: ISO 3384
Compression set: ISO 815 / ASTM D395
Hardness (Shore): ASTM D2240 / ISO 48-4,
Tear strength: ASTM D624 / ISO 34
Adhesion (peel test): VDI 2019
Composites
Tension: ASTM D2290 (split-disc ring), ASTM D3039 / ISO 527
Compression: ASTM D3410 (shear loading), ASTM D6641 (combined loading), ISO 14126 (shear or end loading)
Flexural: ASTM 7264 / ISO 14125
In-plane shear: ASTM D3518 / ISO 14129 (±45° tension), ASTM D5379 (V-notch), ASTM D7078 (V-notch rail)
Through-thickness: ASTM D2344 / ISO 14130 (short beam shear), ASTM D3846 (double-notch compression), ASTM D5379, ASTM D6415 (curved beam strength)
Delamination: J-integral approach (modified DCB-UBM), ASTM D5528 / ISO 15024 (mode I), ASTM D6671 (mixed mode I/II), ASTM D7905 / ISO 15114 (mode II)
Impact: ASTM D7136 (drop weight), ASTM D7137 (compression after impact)
Fatigue: ASTM D3479 (tension-tension), ISO 13003
Other materials and applications
Coated fabrics: ASTM D751
Adhesive bond-lines: ASTM C633 (pull-off tension), ASTM D5656 (thick adherend shear)
Soft ductile materials: ASTM E8 (tension), ASTM E9 (compression), ASTM E139 (long-term creep)
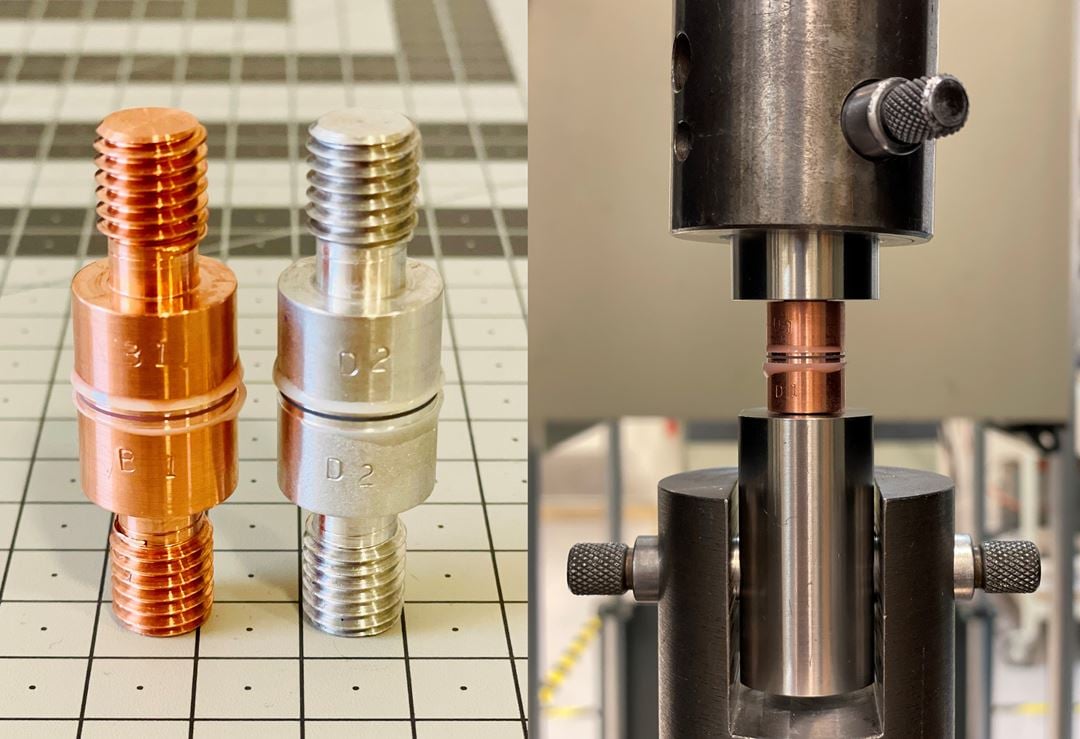
Some relevant publications involving the Polymer and Composite Materials group
A.-M. M. R. Persson, E.L. Hinrichsen, E. Andreassen, On the temperature dependence of the cyclic compression behaviour of a thermoplastic vulcanizate elastomer, https://doi.org/10.1016/j.polymertesting.2022.107650 , Polymer Testing, 2022
A.-M. M. R. Persson, E. Andreassen, Cyclic compression testing of three elastomer types – A thermoplastic vulcanizate elastomer, a liquid silicone rubber and two ethylene-propylene diene rubbers, https://doi.org/10.3390/polym14071316 , Polymers, 2022
F. Grytten, B. F. Sørensen, S. Goutianos, R. K. Joki, J. K. Jørgensen, A micromechanical model of fiber bridging including effects of large deflections of the bridging fibers, https://doi.org/10.1016/j.compstruct.2020.113405 , Composite Structures, 2021
R. K. Joki, F. Grytten, B. Hayman, B. F. Sørensen, A mixed mode cohesive model for FRP laminates incorporating large scale bridging behaviour, https://doi.org/10.1016/j.engfracmech.2020.107274 , Engineering Fracture Mechanics, 2020
A.-M. M. R. Persson, E.L. Hinrichsen, E. Andreassen, Adhesion between thermoplastic elastomers and polyamide‐12 with different glass fiber fractions in two‐component injection molding, https://doi.org/10.1002/pen.25408 , Polymer Engineering and Science, 2020
R. H. Gaarder, J. Smith, O. Welgaard, I. Brovold, A. Duus, Eccentric loading of a 25-m long composite column subjected to a combination of axial compression and transverse gravity loading using a horizontal test method, https://doi.org/10.1177/0967391118823076 , Polymers & Polymer Composites, 2019
H. M. Føre, S. W. Dahle, R. H. Gaarder, Tensile strength of nylon netting subjected to various concentrations of disinfecting chemicals, https://doi.org/10.1115/1.4040562 , Journal of Offshore Mechanics and Arctic Engineering – Trans. ASME, 2019
J. Johnsen, A. H. Clausen, F. Grytten, A. Benallal, O. S. Hopperstad, A thermo-elasto-viscoplastic constitutive model for polymers, https://doi.org/10.1016/j.jmps.2018.11.018 , Journal of the Mechanics and Physics of Solids, 2019
B. Alcock, K. Olafsen, J. Huse, F. Grytten, The low temperature crystallization of hydrogenated nitrile butadiene rubber (HNBR), https://doi.org/10.1016/j.polymertesting.2017.12.027 , Polymer Testing, 2018
B. Alcock, T. A. Peters, R. H. Gaarder, J. K. Jørgensen, The effect of hydrocarbon ageing on the mechanical properties, apparent crosslink density and CO2 diffusion of a hydrogenated nitrile butadiene rubber (HNBR), https://doi.org/10.1016/j.polymertesting.2015.07.007 , Polymer Testing, 2015
G. Perillo, F. Grytten, S. Sorbo, V. Delhaye, Numerical/experimental impact events on filament wound composite pressure vessel, https://doi.org/10.1016/j.compositesb.2014.10.030 , Composites part B – Engineering, 2015
H. Daiyan, E. Andreassen, F. Grytten, H. Osnes, R.H. Gaarder, Shear testing of polypropylene materials analysed by digital image correlation and numerical simulations, https://doi.org/10.1007/s11340-012-9591-7 , Experimental Mechanics, 2012
H. Daiyan, F. Grytten, E. Andreassen, H. Osnes, O.V. Lyngstad, Numerical simulation of low-velocity impact loading of a ductile polymer material, http://dx.doi.org/10.1016/j.matdes.2012.06.020 , Materials & Design, 2012
H. Daiyan, E. Andreassen, F. Grytten, O.V. Lyngstad, T. Luksepp, H. Osnes, Low-velocity impact response of injection-moulded polypropylene plates – Part 1: Effects of plate thickness, impact velocity and temperature, https://doi.org/10.1016/j.polymertesting.2010.05.003 , Polymer Testing, 2010
H. Daiyan, E. Andreassen, F. Grytten, O.V. Lyngstad, T. Luksepp, H. Osnes, Low-velocity impact response of injection-moulded polypropylene plates – Part 2: Effects of moulding conditions, striker geometry, clamping, surface texture, weld lines and paint, https://doi.org/10.1016/j.polymertesting.2010.06.001 , Polymer Testing, 2010