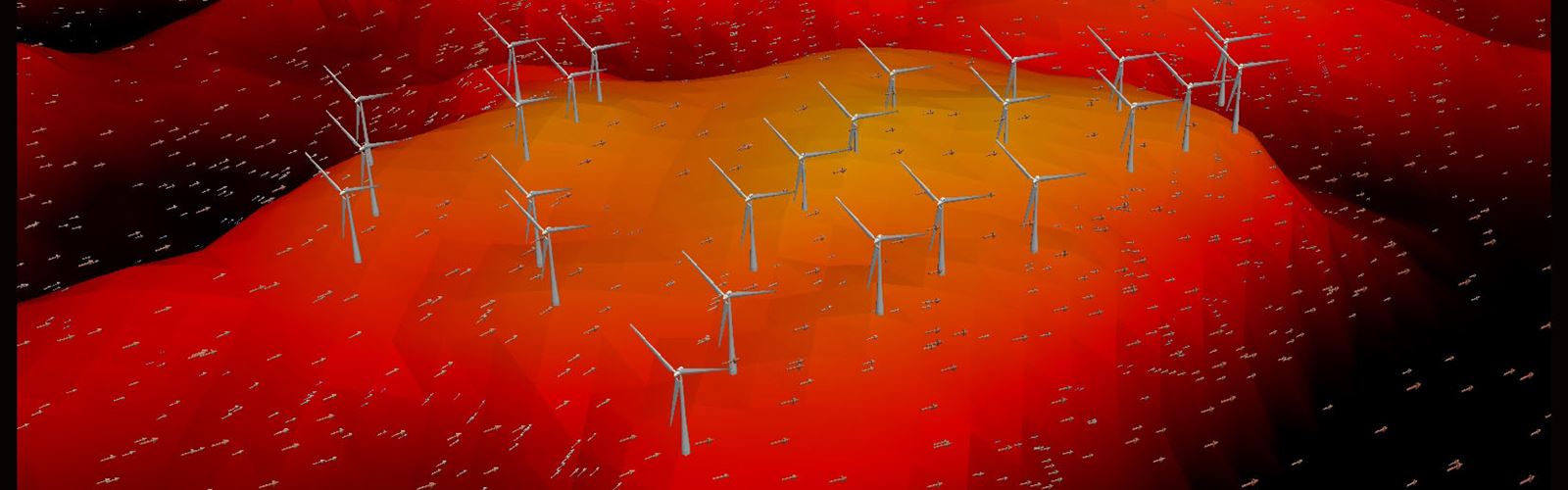
Wind Energy
Wind turbine design and optimization, Wind and power forecast, Wind farm siting, Wind farm layout design, Control system design, Offshrore and onshore wind energy
Our activities int he wind energy sector can be subdivided into the following broad categories:
- Ocean Atmospheric Coupling: In this research field, with a collaboration with the Norwegian Meteorological Institute, an operational uni- and bi-directional Ocean-Atmospheric Model has been developed. The model is now being validated using observational data from sea-buoys and offshore measuring station. Initial results shows the positive effects of a bidirectional coupling approach. The idea is to create a database of different weather condition and characterize marine boundary layer. This part of the work is to be used to understand the effects of marine boundary layer characteristics on the performance of a full scale wind turbine.
- Wind and power forecast: Within this task an operation wind and power forecast system has been developed which provides an hourly forecast of wind and power production for the Bessaker Windfarm. Kalmar filter is being used to assimilate observational data in the prediction system and several ensemble runs are used to quantify uncertainties associated with prediction.
- Wake Modeling: Actuator line model is being used to understand the interaction between atmospheric boundary layer (stratification and wind shear), wakes and complex terrain. Solvers have been developed to simulate the interaction using both RANS and LES approach.
- High Fidelity CFD simulations: These kind of simulations are being used to understand flow around NREL blades, vertical and horizontal axis wind turbines. Wind tunnel data are being used to validate the high fidelity simulations results. The results are then being used to develop simplified models which can be used in an operational set-up.
- Fluid-structure interaction: The CFD tools that have been developed in the group are being coupled to structural solvers. The Fluid-Structure Interaction code has been validated using the famous Turek case. Efforts are also in place to simulate the interaction using a strip theory where 2D CFD simulations are conducted for different sections of a blade and drag and lift forces are fed to the structural solver which computes blade deflections.
More recently we have started developing novel methods to bridge the gap between industrial needs and high fidelity simulation tools.