Separation of CO2 with polymer-based membranes (temperatures below 100°C)
We have extensive experience and expertise in tailoring polymer-based membranes, designing and constructing laboratories and pilot scale facilities, and modelling and simulation of CO2 capture from flue gas, natural gas and biogas. In cooperation with NTNU, we have designed and installed a pilot scale plant at Tiller CO2 laboratory (Trondheim, Norway). Another pilot scale plant will be installed at Norcems cement factory in 2016.
Separation of CO2 with dual-phase membranes
We develop dual-phase membranes with liquid carbonate for separation of CO2 and oxygen from various gas mixtures, such as N2 or H2. The working temperature is 400-700°C.
Separation of H2 for pre-combustion application
Membranes consisting of a thin palladium alloy film applied onto porous support structures have a very high flux and selectivity of hydrogen. The membranes are used in hydrogen separation at temperatures between 350 and 600°C, and are e.g. suitable for use in catalytic membrane reactors in water-gas shift process.
Ceramic membranes for hydrogen separation can be used at higher temperatures (above 600°C) and are therefore suitable for hydrogen production by means of catalytic membrane reactors, such as in reforming of natural gas or biogas.
Separation of O2 for Oxy-combustion application
Membranes of oxygen ion conducting ceramics are used at high temperatures (over 700°C) to separate pure oxygen from air. Combustion of fossil fuels in oxygen, compared to use of air, facilitates CO2 separation after combustion.
Separation of CO2 by membrane contactors
SINTEF has experience and facilities for separating CO2 using membrane contactors. In membrane contactors, CO2 is absorbed in a solvent placed at the permeate side of the membrane. Ongoing activities in this area also include the use of ionic liquids and enzymes for increased CO2 mass transfer across the membrane.
Separation of CO2 with carbon membranes
Carbon membranes have several advantages compared to polymeric membranes, including higher thermal - and chemical stability. In addition, carbon membranes are cheaper and lighter than ceramic membranes. These membranes act as molecular sieves, where the separation of certain components occurs through defined pore structures. The pores can be customized by appropriate choice of precursors and procedures for carbonization, to provide high selectivity for the desired separation process, such as the separation of CO2 from biogas. Carbon Membranes are most effective for industrial processes when prepared as hollow fibres in compact modules. SINTEF has, in collaboration with NTNU, developed expertise in carbon membrane technology.
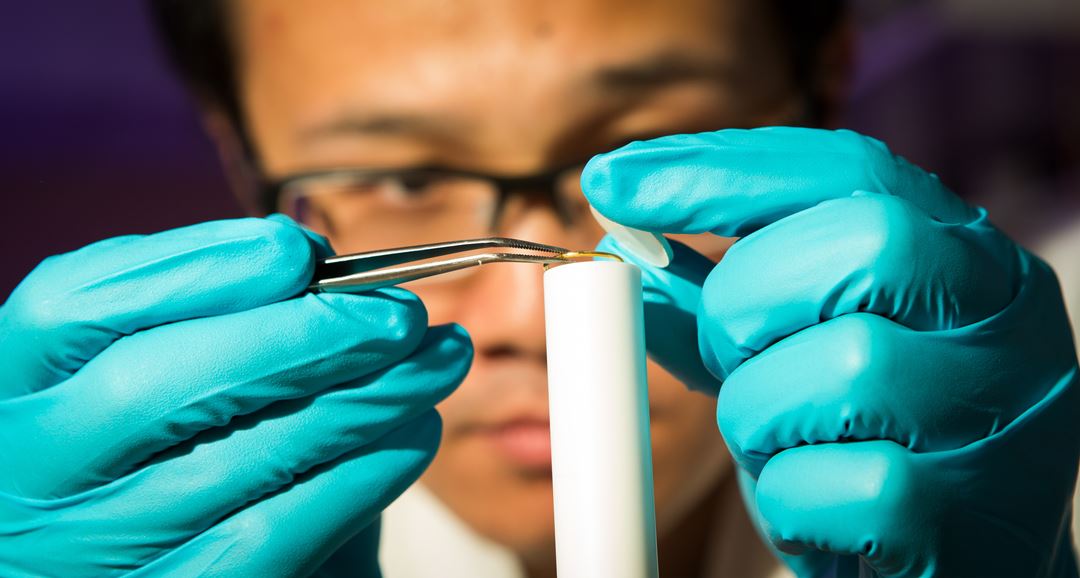