When most people think of offshore oil production, they’re likely to call up images of a big concrete platform, with cranes and a helipad and living quarters suspended over the drilling area. But especially when a petroleum reserve is in deep water, where wells can be 300 metres or more below the ocean surface, an alternative approach called an FPSO can often be the production system of choice.
FPSO stands for floating production, storage and offloading unit, and is a technology that is widely used by Brazil’s petroleum industry, because so many of the country’s petroleum deposits are in deep water.
A key component that makes an FPSO possible is a riser, a long, slender pipeline that hangs like an enormous string below the FPSO, through which fluids, including oil, can be pumped up to the mother ship. Risers can also be used to pump injection fluids or other substances down to the well.
But because an FPSO is floating, the risers, and especially the connections between the risers and the floating structure, are subject to a great deal of force from waves and currents. That’s where Marcelo Caire, a researcher at SINTEF Brasil AS comes in.
“Our main point is to be able to better predict the fatigue life of the riser itself,” Caire said. “We are trying to close the gaps in knowledge and improve industry practices.”
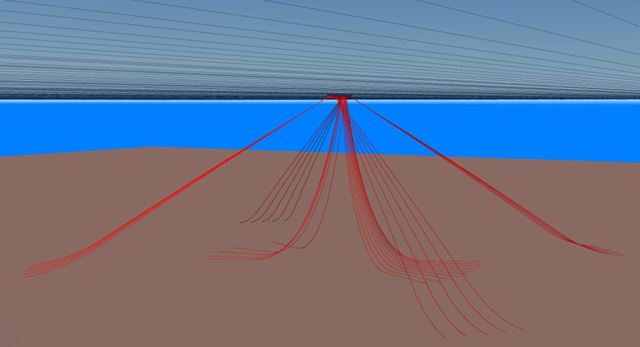
The figure show the risers connecting the well at seabed to the platform. The mooring lines, which keep the platform in the right place, are also shown. The mooring lines are the outer lines in the figure.
Click to open
Improving safety and saving money
Caire’s research explores three areas that are key to understanding the stresses on flexible risers, so that oil companies have a more accurate idea of when to replace them. His work has the potential to improve the safety of the flexible risers while saving money.
Brazil’s main oil company, Petrobras, has scores of FPSOs producing oil from deep water areas, where each FPSO may have as many as 50 flexible risers, each one of which can be 2.5 km long or more. These risers are thought to have a lifetime of 20-25 years.
“Petrobras has many risers that have been operating for many years and they are now reaching the end of their design life,” Caire said. “If we can assess the risers using a better approach, we think that risers could be in operation for a few more years, which could be a huge cost savings.”
Caire’s work could help in the design of future installations, too. In fact, the use of risers is likely to continue to grow with Brazil’s development of ultra deep water petroleum reserves called the pre-salt deposits. These oil reserves can be as deep as 2000 metres or more and lie underneath a cap of salt, which explains their name.
Providing a dynamic simulation
Some of the first FPSOs in Brazil came into use in the Campos Basin in the late 1980s, although the flexible riser system was first used in Brazil in 1977, in a different production system for an area of the Campos Basin called the Enchova Field. At that time, engineers were limited by computational power and only considered the stresses that a flexible riser would experience from waves and currents in what is called a decoupled analysis.
The term decoupled refers to the fact that the analysis looks at only the riser, as if it had been decoupled or unhooked from its attachment to the FPSO.
But Caire says that it’s possible to get a much clearer idea of how much stress a flexible riser is under by also considering how the movement of the riser affects the FPSO – and vice versa.
Caire’s investigation is the development of efficient computational methods for the fully coupled global dynamic analysis – global because it considers a universe of forces acting on both the riser and the FPSO unit, and dynamic because it tries to account for the dynamic interaction between the structure and the riser.
For example, the damping and inertial effects of the riser and mooring system may influence the dynamic response of the FPSO and its mean position.
Providing a dynamic simulation of both the moorings and risers means that there is more accurate information on forces for the floater simulation, Caire says. Then the floater simulation provides correct information on its movement for the mooring and riser simulation, in an interactive way – which combined leads to better prediction of the riser response.
“When these risers were designed, the industry in Brazil used the decoupled approach,” Caire said. “But the decoupled approach is less realistic.”
Artificial neural networks
Conducting a fully coupled global dynamic analysis isn’t simply a matter of loading a mountain of information into a computer and waiting for an answer to pop out, however. The analysis is very complex, and demands a great deal of computational time.
For that reason, Caire and his colleagues are enlisting a computational approach called an artificial neural network, which is actually a computer programme or algorithm that tells the computer how to think.
As its name suggests, a neural network mimics the way the human brain “learns” – except in this case, the neural network is said to be trained.
Caire says the neural network is fed a series of different factors and responses to those factors. For example, the network might be given information about different waves in the Campos Basin along with information that describes how the flexible risers respond to the different waves.
“So for some situations the neural network knows the input and then knows the output (the response),” Caire said. “In this way we train it so that we can use it to predict future responses for which we don’t actually know the answer.”
Because the network can “learn” from what it is given, it can cut computational time, he said, while still capturing the dynamics of a fully coupled analysis
The highest loads
Another area that Caire is extremely interested in is the place where a flexible riser is attached to the FPSO with an attachment called a bend stiffener – because this is the area that can experience some of the highest stresses and loads in the system.
“We are trying to understand how the bend stiffener will affect the riser response, in terms of stress and strains,” he said.
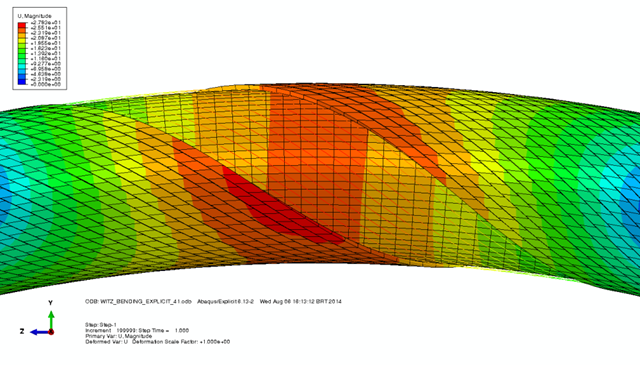
The figure shows the deformations of one of the layers of a flexible riser. It is the result of a simulation run by Caire and illustrates “the tough life” of a riser.
Click to open
Caire says the top connection is a critical area of the riser in terms of failure mechanisms and fatigue. The bend stiffener eases the transition between the flexible riser and the rigid support of the FPSO, he says, by limiting the curvature in the riser and stresses in that area.
But the bend stiffener is made out of polyurethane, and researchers like Caire still need to know more about how the material behaves and its stability in the marine environment.
“We are performing a series of mechanical tests (tensile, compressive, stress relaxation and creep) with small scale samples to characterize the nonlinear viscoelastic response,” he said. Viscoelastic means that a material has some viscous properties, like the viscosity of honey, and elastic properties, where a material that is stretched returns to its original shape, like a rubber band.
A viscoelastic response can be strongly affected by temperature, which is another factor the researchers have to consider.
Using these tests, the researchers have developed a model that reflects the interaction between the bend stiffener and the flexible riser in the unpredictable conditions of the open ocean – using the information from the fully coupled global dynamic methodology that Caire has developed.
This approach is much more sophisticated than what the industry currently uses, he said.
“The industry only considers elastic response, which can lead to mistakes or uncertainties,” he said. “What we are doing is closing this knowledge gap and seeing how important this effect is in assessing the top connection” between the riser and the FPSO.