“The first thing we have to do is get an overall picture of the wells in question, their condition, maturity and the cost of the technology”, says Kjetil Midthun at SINTEF.
“Then we can generate a database, and after that develop a planning tool designed to reduce costs. The industry and consultancy companies are showing great interest and we have 19 stakeholders participating in this project. These are costs that Norway has to bear and the time is right to get the preparatory work started”, he says.
Storing up problems for the future
Thousands of oil wells have been drilled on the Norwegian shelf. They can be compared to man-made ‘drinking straws’ made of cement and steel, each extending for many kilometres below the sea floor. Most of these wells are still in production, but when they are finally abandoned they will have to be plugged to prevent them leaking and causing environmental damage.
FACTS:
- The ECOPA project (ECOonomic analysis of coordinated Plug and Abandonment operations) will extend from 2015 to 2018.
- The project participants are SINTEF Technology and Society, SINTEF Petroleum Research, NTNU Industrial Economics and Technology Management, and a total of 19 other stakeholders.
- The project is divided into two parts: 1) Data capture and generation of a database. 2) Development of a planning tool designed to reduce costs.
- The project is fully financed with NOK 8 million from the Research Council of Norway via its Petrosam2 and Petromaks2 programmes.
In the same way as the Norwegian state takes 78% of oil revenues in tax, it must also bear an equally large share of the costs involved in activities such as exploration and the plugging of wells. This means that the state (we’re talking about the Norwegian taxpayer here) will have to bear the greater part of the plugging costs, estimated to be about NOK 900 billion.
Both oil companies and researchers have be busying themselves trying to find out how these costs can be reduced, leading to the current launch of a project called ECOPA .
The project is fully funded with NOK 8 million from the Research Council of Norway and will combine economic analysis with technological insight. Hopefully it will come up with answers to the following questions: Is it possible to reduce plugging costs? Can the plugging process be simplified and improved? Can plugging be carried out from vessels instead of drilling rigs? What new technologies are required?
Getting the big picture
“Everyone knows that plugging is an immature and very expensive process”, says Midthun.
“Our information database is somewhat limited”, he says. “Very little detailed information is available about well plugging. For example, when the plugging operation took place, and how. Nor are we aware of factors such as whether or not equipment on the sea floor has been removed, when currently productive wells will be plugged, or what the total costs of the plugging operation will be. For this reason it’s important for us to get as big a picture as possible before we proceed”, he says.
Many offshore operators and research centres are participating as consultants in this project. The multidisciplinary team of social science and petroleum researchers from SINTEF and NTNU want to establish a close working relationship with both the industry and the authorities. This is because it is they that are in possession of important sources of information. They also share the researchers need for a better overview of the challenges that everyone is facing.
“We also have to review current legislation, regulations and standards”, says Midthun. “For example, a secure cement plug on the Norwegian shelf typically has to be 100 metres long, although the standard on the UK shelf is more commonly 100 feet (approx. 30 metres). Such differences result in a variations in plugging costs, and it will be interesting to find out what this will mean in terms of the final bill the Norwegian taxpayer has to pay”, he says.
The plugging process
Once the overall picture and information database are in place, the project participants will be able to start developing the planning tool that will be needed to identify bottlenecks in the system. Where will improvements be needed? What plugging technologies will result in the greatest savings?
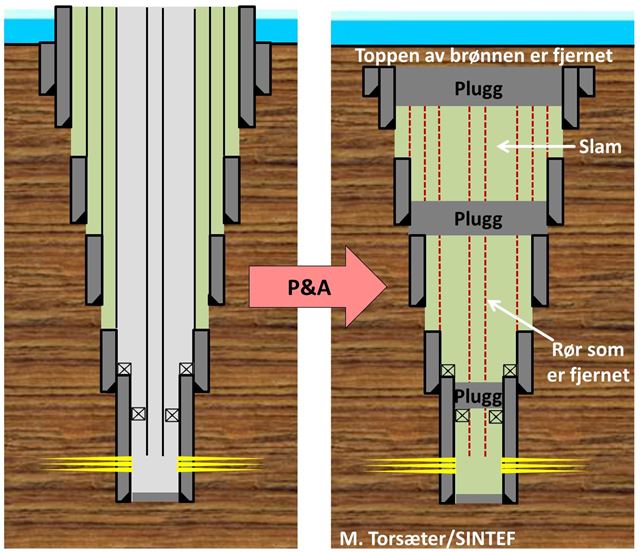
A schematic illustration of permanent well plugging. Plugs are placed at selected places in the well, and slam is filled in between. Some of the original pipes in the well have to be pulled up, and the top of the well must be removed. Figur: SINTEF
“Maybe we’ll have think out of the box here”, says Midthun. “There may be opportunities for savings if plugging campaigns are better planned, if licences work closer together and if their scant and costly resources are better exploited. We aim to use the planning tool to quantify the potential benefits that can be achieved by more plugging campaigns and increasing levels of collaboration”, he says.
“What is plugging really all about?”
“Plugging involves filling in the well with a sealing material at selected locations. The challenge is to ensure that it is completely sealed. In many cases, much of the original steel casing and cement in the well have to be removed in order to achieve an adequate seal”, says Midthun.
“And how is this carried out?”
“Normally by using large rigs costing several million kroner per day. This is why we will be trying to find out whether it is possible to plan to plug all the wells in a given area at the same time using a single rig, or whether it might be possible to transfer plugging operations to a lighter, and less expensive, ship-like vessel. Maybe this will lead to significant cost reductions”, says Midthun. “We’re now looking forward to getting the project up and running”, he says. As far as we know, this process hasn’t been undertaken anywhere else in the world, and may result in providing Norwegian companies with a competitive edge in the world market.”
The database is planned to be in place in 2017, and in 2018 a report will be published containing all the information and a final model designed to analyse individual operations.