Norwegian ferroalloy, silicon and silicon carbide producers have set up an interdisciplinary expert group and asked the members to study how ultrafine airborne dust is created in their plants and the potential effects of exposure to such dust. The group will also study possible protective measures.
“This is very first time that occupational hygienists, occupational physicians, toxicologists, metallurgists, production engineers and occupational psychologists have joined forces in a study of this type. The project has aroused international interest even before it has started,” says SINTEF scientist Ida Kero, one of the experts who took the initiative to launch the ground-breaking study.
Biological studies and tests of masks
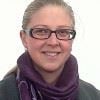
SINTEF scientist Ida Kero is one of the experts who took the initiative to launch the study.
Click to open
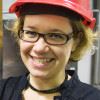
The project is managed by Gabriella Tranell who is a professor at NTNU.
Click to open
Kero, who is a process metallurgist herself, explains that several process stages in the ferroalloy, silicon and silicon carbide industries create dust, some of which is ultrafine. In the recently launched project, SINTEF and NTNU will find out how the dust is formed. Researchers from the two institutions will also characterise ultrafine dust from a number of sources.
The National Institute of Occupational Health will take over the characterised material and study the biological effects of ultrafine dust on human cells in the laboratory.
The University Hospital of North Norway in Tromsø and St. Olav’s Hospital in Trondheim will also investigate how well traditional face-masks protect users against ultrafine dust, and study psychological factors that affect the use of masks in industry.
“For the industry, this is an important project to ensure that there are no unknown, health related challenges connected to the dust from our processes,” says senior metallurgist Birger Andersen of Fesil Rana Metall AS, adding that ”If there are any such problems, we need to identify them and do something about them.”
Less dust in the future?
SINTEF and NTNU’s part in the study is concerned with basic physics, chemistry and thermodynamics.
“Once we understand how ultrafine dust is formed, we can, if necessary, adjust the processes so that they produce less dust,” says Ida Kero.
Joint effort
The pioneering project is a joint effort, carried out by Norwegian research and industrial partners. It is partly financed by the Research Council of Norway’s Nano 2021 programme. Other partners on the financial side include Washington Mills, Saint-Gobain, Elkem, Eramet Norway, Fesil Rana Metall, Glencore Manganese, Wacker and Finnfjord.
The project is managed by Gabriella Tranell of NTNU and will last for four years.
It is an Industrial Competence Project (KPN in its Norwegian acronym) and the Research Council of Norway has great expectations for the project.