An international research team recently completed a three-year EU project called DESCRAMBLE (Drilling in dEep, Super-CRitical, AMbients of continentaL Europe). Together, the project team has drilled a test well in a geothermal field in Tuscany in Italy. The Italian company Enel Green Power, a global producer of green energy, is heading the project, with SINTEF as its research partner. Together they are attempting to harness the natural forces found three kilometres closer to the Earth’s core.
Geothermal Energy Facts:
For each kilometer moving towards the Earth's core, the temperature rises, and at the inner end of the core it reaches 5,000 degrees Celsius. The heat is residual heat from the soil's origin and from the decomposition of radioactive substances.
A number of countries today utilize the natural heat of the earth by transforming it into electrical energy. This is done by drilling in the ground and then extracting heated water that runs through turbines on a power plant.
The power plant produces electrical energy and the waste heat is used for heating. A common geothermal well holds an ambient temperature of 350 degrees Celsius.For a geothermal well to be defined as supercritical, the water in the well must keep at least 374 degrees Celsius and have a pressure of 220 bar. If scientists manage to capture the supercritical water, one well may be enough to power a power plant that today requires ten wells. This will reduce costs and also minimize the footprint for geothermal energy production.
Democratic and environmentally friendly
Geothermal energy is a democratic source of energy based on its existence throughout the globe and it can be exploited independently of conditions on the earth's surface, such as wind and weather.
However, areas close to the edge of a soil plate are better suited to collecting geothermal heat. In Europe, Italy, Iceland and Turkey, are best suited. Earth heat is considered renewable energy. The geothermal well does not release CO2, but the operations around the well, such as drilling rigs driven by diesel-powered aggregates, releases some CO2.
The borehole is the world’s hottest geothermal well in a non-volcanic area. Because terrestrial heat is encountered close to the surface in Italy, the country is rich in areas suitable for geothermal drilling – with searing temperatures reaching 500-600 degrees Celsius, resulting in supercritical water that the researchers are hoping to discover. And they have very good reasons. If they can succeed in exploiting the energy in this water, they can drill geothermal wells that are ten times as effective as those currently in operation. This has the potential to reduce costs dramatically and pave the way for a fantastic energy future based on purely natural resources. However, in its supercritical phase, the liquid is corrosive and attacks any drilling equipment that encounters it.
Supercritical energy bomb
We are faced with a lot of big challenges, but we’ve come a long way,” says Magnus Hjelstuen, Research Manager at SINTEF Harsh Environment Instrumentation.
In its supercritical phase, the liquid is corrosive and attacks any drilling equipment that encounters it.
The measuring equipment SINTEF has developed as part of this project is a so-called “wireline logging tool” that can measure downhole temperatures and pressures. Such measurements are crucial in the search for the extremely energy-rich supercritical water. Temperature and pressure data indicate when the drill bit has entered a zone containing such water, and the well’s geothermal properties (both the maximum temperature and temperature changes caused by drilling) will tell us how much energy the well can produce.
Since electrical cables do not function at temperatures over 350°C, SINTEF’s measuring equipment is battery-powered. The temperature is logged deep in the borehole and is read off when the device returns to the surface.
In its supercritical phase, the liquid is corrosive and attacks any drilling equipment that encounters it.
This is no simple task. At two to three kilometres into the Earth’s interior the temperature and pressure rise enormously. Something very special happens when the temperature reaches 374 degrees and the pressure is 218 times the air pressure at the surface. We encounter what we call supercritical water. This water is in a physical state that progresses from liquid into gas – and from there into a supercritical phase, in which it is neither.
It is this special form of water, as yet undiscovered, that the researchers are looking for. To reach the conditions that make it supercritical, the water must have a temperature of at least 374°C, under pressures of 200 bar.
“A water column at room temperature must be taken to a depth of 2.2 kilometres below the surface to reach a pressure of 220 bar,” Hjelstuen explains.
But when the temperature of the water rises, its density falls. This means that we must go even deeper to pass 220 bar and attain supercritical conditions. If the water is contaminated with gases and minerals, which is always the case in a geothermal well, the temperature must be higher still for the water to become supercritical.
Extreme equipment
SINTEF uses electronics and sensors with extreme capabilities. Some of the components are in common use, while others are still at the prototype stage. The challenge for the Norwegian researchers has been to combine the sensors and electronics, and then develop computer software that enables the components to function together.
“Our challenge has been to find a combination of existing components which can perform optimally within our limitations in terms of instrument length, weight and diameter – not least in view of the environment the equipment will encounter in the well,” says Hjelstuen.
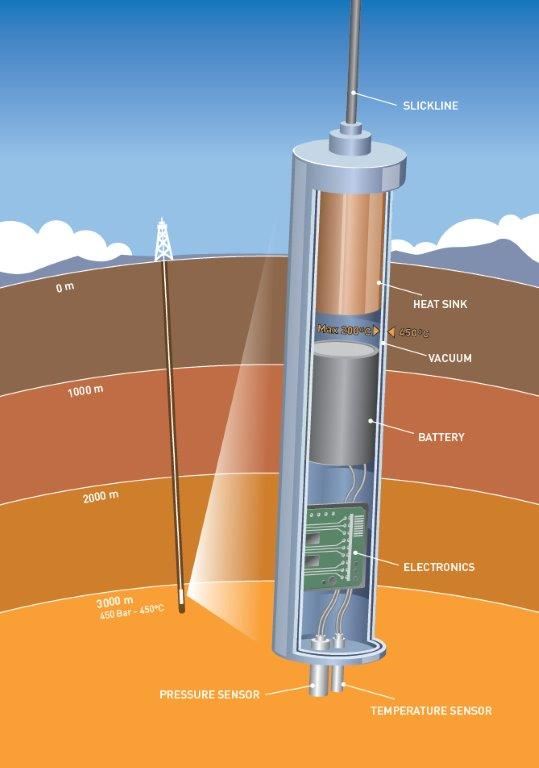
Illustration of the well now drilled in Lordello. Copyright: Doghouse
The instrument is 2.6 metres long weighs 50 kilograms, but has a diameter of only 76 millimetres.
“For example, we use a micro-controller which functions at temperatures up to 300°C. This is only available as an early prototype (engineering sample). So we’ve been working closely with the manufacturer to get it to function the way we want it to,” he adds.
Intense pressure and temperature
At present, the limiting temperature for electronics is around 250°C, and this means that the range of components available is very restricted. The number of suitable batteries is also not large. For example, the most robust batteries on the market work at temperatures of only 70 to 200°C and would explode if subjected to a temperature of 215 degrees. So making measuring equipment can be a challenging process.
“Since we begin drilling at normal surface conditions, the temperature on a winter’s day may be as low as 0°C to start with, rising to over 400°C at the bottom of a well. Tackling such fluctuations makes enormous demands on the equipment. We’ve created a sort of “reverse Thermos flask” in which the inside temperature is kept below 210 degrees so as to reduce the strain on the equipment,” says Hjelstuen.
The sensors are trialled and tested before being shipped to the field.
“At every stage an enormous amount of testing must be carried out in a way that as closely as possible simulates the environment our instruments will encounter in the well. Among other things we have used a furnace at Raufoss to test the technology at temperatures up to 450°C.
Enormous potential
In the process of harnessing the energy in the supercritical water, the researchers have made good use of the Norwegian petroleum industry’s experience in drilling deep oil wells. The exploitation of geothermal heat has much in common with oil recovery. Petroleum technologists are therefore included in the team. However, whereas we have for many decades succeeded in exploiting the potential found in petroleum resources, nobody has yet managed to harness supercritical water.
“If we can succeed in exploiting geothermal heat there will be enough of it to supply the entire population of the planet with energy for many generations. There are nuclear power plants where water that meets the conditions for supercritical water is fed through turbines, so we know that we can succeed in exploiting the energy in such water once we have managed to extract it.”
In the project’s deepest descent into the Earth, the research team carried out measurements at a depth of 2810 metres. Here the temperature reached 443.6°C.
Going even deeper
“We were able to test our instrument and it withstood the high temperatures, which was a milestone in itself. Unfortunately we did not find a site where water flowed into the well. We’re now working on a new EU funding application so that we can take the project to the next level. We want to drill even deeper – to 3.1 kilometres – where we hope to find a water source from which we can test energy production,” says Hjelstuen.
If they do not find a water source, they will have to drill an additional well that can be used to inject water into the rock formation. This water can then be extracted via the first well. In any case, since they are now planning to penetrate even deeper, they need to develop equipment that can withstand even greater heat loads.
“It means a lot to SINTEF to be involved in this energy exploration. Making sensor measurements in places where they have previously been impossible is an ideal project for us. We’re now planning to develop equipment that can withstand temperatures of up to 600 degrees Celsius,” says Hjelstuen.
At present the equipment can measure pressure and temperature, but in the next phase the plan is to develop devices that can recover samples of liquid from a well for subsequent analysis.
“We are setting ourselves ambitious goals, but we are sure that we will succeed,” says Hjelstuen.
This has been done by Norwegian researchers:
- Mechanical design and choice of metals that will work in the extreme environment.
- Electronics design for very high temperatures. Particular focus on measuring the highest possible temperature while logging data with the lowest possible power consumption.
- Testing of different battery technologies. Due to the chemicals in the batteries, they will only work within a limited temperature range. The batteries need to operate from 70-200 ° C. The equipment must also operate at normal room temperature.
- Finding sensor solutions that can work in demanding environments. Some components are therefore shielded by their own hot shield.
- Testing of sealing- solutions and development of test methodology that allows simulations of the tough conditions in the well. (up to 450 bar and 450 ° C). The instrument must use metal drawings (o-rings can only be used up to about 325 °). Several attempts had to be done before the researchers found an optimal solution for measuring the high pressure and temperature at the same time.
- Thermal simulations to estimate the thermal flux through the heat shield, this to dimension the volume required by the heat sink material (copper) inside the measuring instrument. This also controls the weight, length and size of the equipment, which should be as low as possible.