“In our tests, we’ve replaced up to 40 per cent of the cement normally used in concrete”, says Senior Researcher Per Anders Eidem at SINTEF Helgeland, located north in Norway.
By using a finely-powdered slag as a binder additive, researchers have achieved significant reductions in the climate footprint of concrete.
The method has resulted in up to a 95 per cent reduction in greenhouse gas emissions, compared with the use of traditional cement. Eight per cent of global greenhouse gas emissions are derived from concrete manufacture.
“Cement manufacturers acknowledge that there is a need to do something about the climate footprint of their product, and thus also to make concrete more sustainable”, says Eidem.
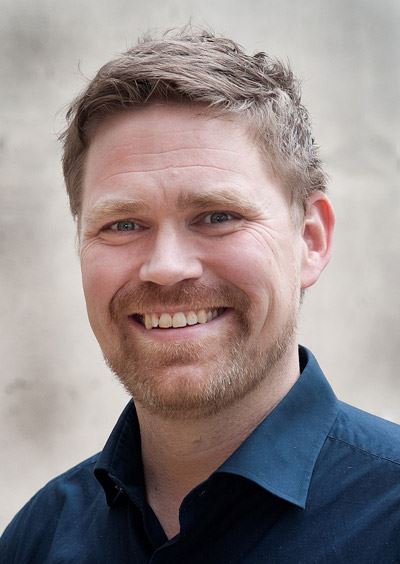
Per Anders Eidem at SINTEF
From industrial fill to a sustainable additive
Per Anders Eidem is conducting research into concretes in which a major part of the traditional cement binder is replaced by a slag material called Silica Green Stone, or SiGS. The project is called VALSiGS. SiGS is a slag waste resulting from the manufacture of silciomanganese, which is a key component in steel production.
“The SiGS slag is a by-product, traditionally used as an industrial fill, and manganese manufacturers Eramet needed to find an alternative use for the material”, says Eidem.
“Adding such by-products to concrete is just one of a number of initiatives that the cement manufacturers are trying out in order to address their climate footprint”, says Eidem. “Another has been the use of flue ash derived from coal-fired power stations, but access to this material is now becoming more restricted, and it’s unlikely that much more will become available”, he explains.
Slag from iron smelting is another by-product that is used in cement.
“The SiGS slag that we’re studying now has some similar properties to that which we derive from the production of iron in blast furnaces”, says Eidem. “When ground down to a fine powder, the slag takes on binding properties that enable it to react and replace some of the cement component”, he explains.
A fine powder
In order to conduct tests on the SiGS slag, SINTEF and Eramet have joined forces with concrete paving specialists Aaltvedt Betong and prefabricated slab manufacturers Block Berge Bygg.
“We ground down the slag in order to find out how it would behave as a cement substitute”, explains Eidem. “Eramet cooled down the SiGS and ground it down to the same particle size as the cement. Then they made both a dry concrete mixture, similar to that used to cast paving stones, and a wet mixture, such as that used in building constructions”, he says.
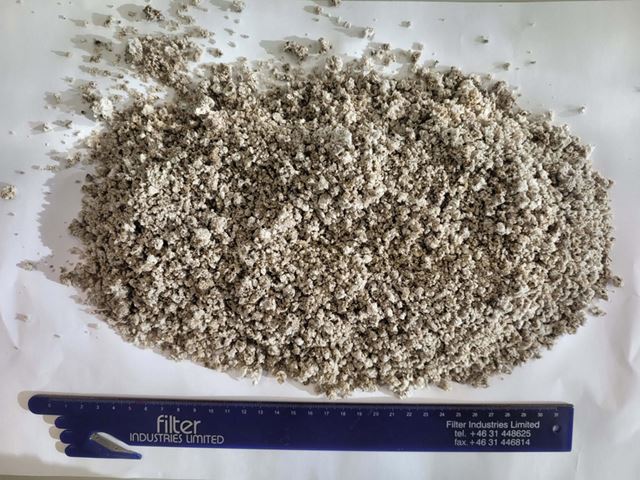
This is the powdered SiGS slag that can act as a substitute for cement in concrete. Photo: SINTEF
Strong enough
“In both cases, we obtained very good results”, says Eidem, referring to strength measurements made on the concrete mixes. The researchers performed their tests after 28 days, which is the standard period for concrete strength tests.
The concrete increases in strength as it ages, far beyond the 28-day period. At present, the researchers’ conclusion is that the ‘SiGS concrete’ is strong enough to be used for the same purposes as concrete containing pure cement without any slag additives.
“Its early strength is lower, but after 28 days this increases so that it becomes just as strong as so-called environmental cement – at least, in the case of the dry concrete mixture”, says Eidem.
The results were good, even with as much as 40 per cent of the cement replaced by SiGS. However, in the next stage of the project, when the SiGS cement will be tested at a larger scale, it is likely that a smaller proportion of the SiGS slag will be incorporated into the mixtures than in the initial experiments.
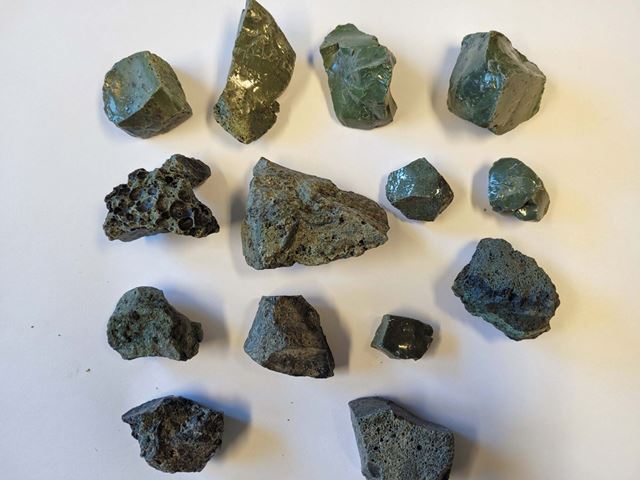
Silica Green Stone, or SiGS, is derived as by-product of silicomanganese production. Photo courtesy of Eramet
Ninety-five percent emissions reduction
The degree to which SiGS cement mixtures can be described as more climate-friendly than pure cements depends on many factors, including how the electricity used in their production is generated. However, a first estimate indicates that the carbon footprint of pure cement is between 20 and 25 times greater than for SiGS mixtures. In other words, the use of SiGS can result in a 95 per cent reduction in greenhouse gas emissions, compared with traditional cement.
“SiGS offers significant benefits”, says Eidem.
SiGS and binding agents from other suppliers are now going to be tested as part of some major pilot projects. “This will be carried out as part of an overall project designed to develop more climate- and eco-friendly roads”, says Christian John Engelsen, who is a Chief Research Scientist at SINTEF Community.
“The slag will undergo further testing with a view to establishing sustainability in both the supply chain and materials use linked to roadside constructions”, says Engelsen.
Facts about the project:
The participants in the VALSiGS project, formally known as ‘Forbedret bærekraft for betong gjennom verdirealisering av Silica Green Stone’ (Enhanced concrete sustainability enabled by the commercialisation of Silica Green Stone) have been Eramet (the Project Owner), SINTEF Helgeland and SINTEF Industry, the University of Agder and industrial sector partners Aaltvedt Betong and Block Berge Bygg.
The aim of the project has been to develop an eco-friendly binding agent, able in part to replace the cement in concrete mixtures and thus reduce the environmental footprint of the concrete. The project has found that the climate footprint of concrete is reduced by about 0.85 per cent for every percentage point by which traditional cement is replaced by SiGS.
If it were possible to utilise all the SiGS currently available in Norway, the full potential in terms of energy saved would be about 227 GWh annually, accompanied by a reduction in CO2 emissions of about 180,000 tonnes per year.
The VALSiGS project has confirmed that SiGS can be used to replace traditional cement at least in part in both wet and dry concrete mixtures.
SiGS and other binding agents are being further tested as part of a so-called Green Platform project called ‘Bærekraftig verdikjede og materialbruk i vegbygging’ (Sustainable value chains and materials use in road construction). Project participants include the Norwegian state road construction and operating company Nye Veier and the infrastructure business cluster VIA. The aim here is to test and commercialise innovative approaches.