Norway has high electric vehicle density on its roads, and those EVs are packed full of conductors. These conductors contribute significantly to the overall weight of electric vehicles.
“Historically, conductors have been made of copper, because the metal has excellent conductivity, malleability and strength,” says Jørgen A. Sørhaug, who is employed at SINTEF Manufacturing.
Copper is therefore very well suited as a conductor, but it has one drawback. The metal is also quite heavy. It has a high mass density, as scientists would say.
“So copper’s weight contribution in an electric vehicle is significant,” says Sørhaug.
Replacing copper with aluminium
The weight affects the energy efficiency of EVs, and thus the range. It would be really advantageous if we could reduce this weight. So what can we do if we want to use less copper?
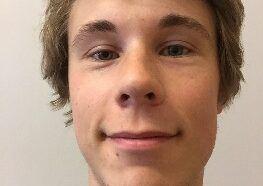
Jørgen A. Sørhaug. Photo: NTNU
“Aluminium is a good alternative to copper, since its conductivity is almost as good as copper’s, and it has good malleability and strength when used in alloys. Aluminium is also much lighter than copper,” Sørhaug says.
This means that if we can replace some of the copper in conductors with aluminium, vehicles will be both lighter and more energy efficient. This was part of Sørhaug’s recent doctoral work at NTNU and is precisely what he and his colleagues are now working on.
They make electrical conductors by joining copper and aluminium into “hybrid” conductors.
“In our project, we produced hybrid power conductors of copper and aluminium by welding, and tested and examined them carefully afterwards.”
Cold welding increases conductivity
Making this kind of high-quality conductors is technically demanding. But cold welding can help to utilize the good properties of the metals without necessarily compromising their conductivity.
During the welding process, aluminium and copper are mixed at the atomic level on the contact interface, usually mixing better the higher the temperature. This often results in brittle crystals, called intermetallic compounds, being formed from the metals, which have poorer conductivity than the pure metals. You therefore want to have as few of these crystals as possible, so welding at high temperatures is a disadvantage – because both conductivity and strength decrease.
“We therefore investigated cold welding as an alternative method, using the patented hybrid metal extrusion & bonding technique,” says Sørhaug.
This technique, with the acronym HYB, was developed at NTNU. The researchers subsequently examined the welds using various forms of electron microscopy, including methods with names like precession electron diffraction, high-resolution scanning transmission electron microscopy (TEM) and X-ray analysis. Fortunately, you and I don’t need to learn what all these methods involve, but the results are encouraging.
“We’ve observed that the HYB technique is better suited for joining aluminium and copper than other cold welding techniques. Thin and slow-growing intermetallic layers form at the interface between the metals. This is beneficial, because then the mechanical and electrical properties of the conductors are less prone to changing.”
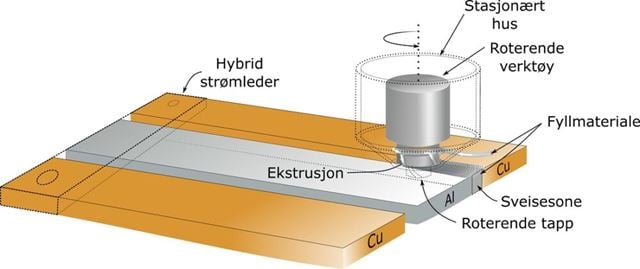
HYB. Schematic overview of the welding procedure. Illustration: NTNU Translation of terms: Hybrid strømleder: hybrid conductor; Stasjonært hus: stationary housing; Roterende verktøy: rotating pin; Fyllmateriale: fill; Sveisesone: welding zone; Roterende tapp: rotating pin tip; Ekstrusjon: extrusion
Why is heat a problem?
More research is needed before aluminium can replace some of the copper. One drawback is that pure aluminium is mechanically weaker than copper.
We can increase the strength of aluminium by making alloys, where we add carefully measured doses of other substances called “alloying elements.” The alloy is also thermomechanically treated. It is rolled or shaped in another way before being heat-treated again.
“But alloyed aluminium is often sensitive to high temperatures, and its strength typically weakens when welded. So we’ve also investigated what causes this strength reduction on an atomic scale, and how we can improve the alloys so that they can tolerate heat better,” says Sørhaug.
Further aluminium research
The project that Sørhaug has been working on ends this year, but NTNU and SINTEF have been awarded a new project to continue studying the cold welding of aluminium and copper. The goal is to achieve better temperature control and tailor plastic deformation on a nanoscale.
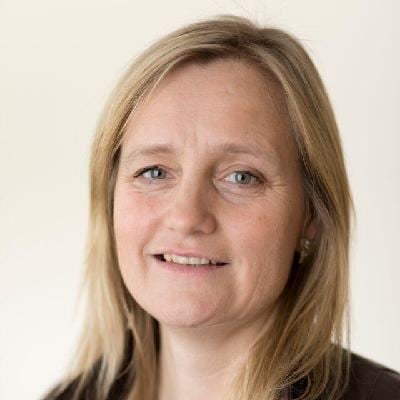
Randi Holmestad. Photo: NTNU
The research team includes industry collaborators Hydro ASA, Corvus Energy AS and Professor Grong AS.
“We plan to build on Sørhaug’s research to create stronger cold-welded connections between aluminium and copper,” says Randi Holmestad, a professor of physics at NTNU.
Holmestad has also been one of Sørhaug’s supervisors during his doctoral work, along with Per Erik Vullum, a senior research scientist at SINTEF Industry.
“By microstructuring and optimizing the welding geometry, we’ll create a nanostructure in the interfaces that improves both strength and conductivity. This is especially true for electrical applications like the ones found in the battery systems from Corvus Energy,” says Holmestad.
NTNU and SINTEF are collaborating with industry partners. This will lay the foundation for producing new advanced multi-material components and products in Norway.
Together, the work could one day contribute to lighter and more efficient electric vehicles.
References:
Aksel Elkjaer, Jørgen A. Sørhaug, Geir Ringen, Ruben Bjørge, Øystein Grong, Electrical and thermal stability of Al-Cu welds: Performance benchmarking of the hybrid metal extrusion and bonding process, Journal of Manufacturing Processes, Journal of Manufacturing Processes, Volume 79, 2022, Pages 626-638. https://doi.org/10.1016/j.jmapro.2022.04.029
Jørgen A. Sørhaug, Aksel Elkjaer, Elisabeth Thronsen, Tina Bergh, Øystein Grong, Per Erik Vullum, Randi Holmestad, Al-Cu intermetallic phase growth in hybrid metal extrusion & bonding welds exposed to isothermal annealing or direct current cycling, Materials & Design, Volume 240, 2024, 112867. https://doi.org/10.1016/j.jmapro.2022.04.029
Collaborative and Knowledge-building Project (KSP) through the Research Council of Norway: 353008 Tailoring Metallurgically bonded nanoscale interfaces between Al, Cu and Ni involving Deformation-enhanced diffusion (MAD)