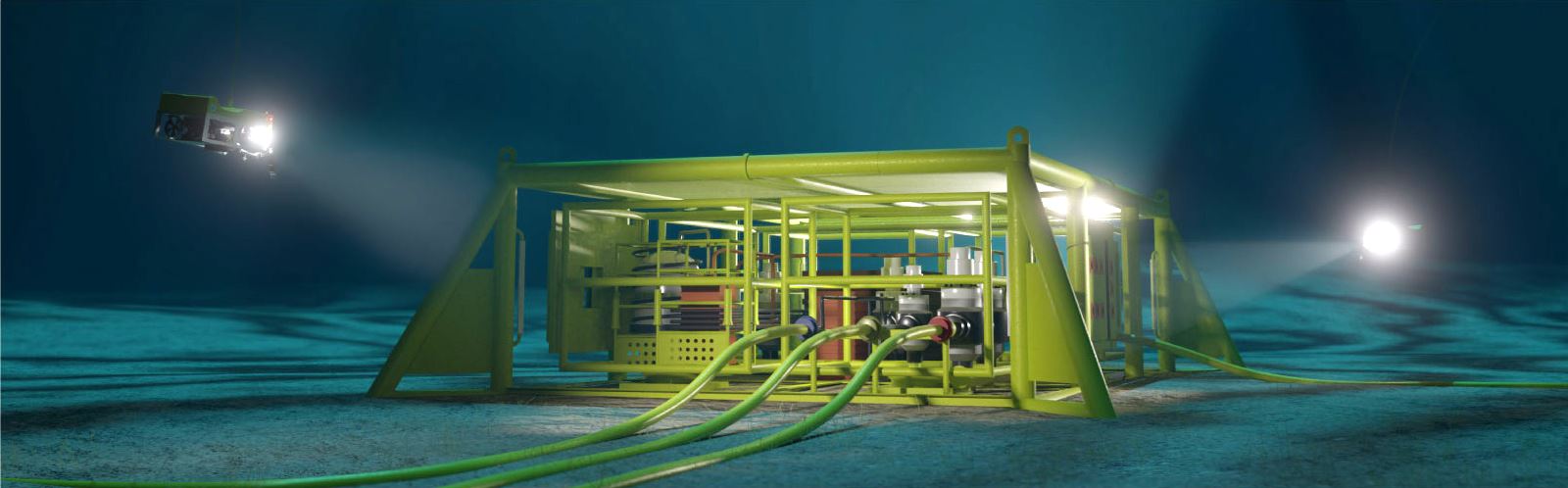
Subsea power supply
Main results
In order to determine relevant materials for the project, an extensive survey of the use of polymer materials for electrical insulation materials in high voltage subsea equipment was performed. Some materials commonly not used but with promising properties were also included, such as syndiotactic polypropylene (sPP). This material could for instance be used as an alternative to cross-linked polyethylene (XLPE) facilitating higher service temperatures and simpler processing.
Five different grades of polypropylene (PP) materials were selected and examined in respect of their thermal, dynamic and morphological properties A sPP material, manufactured by Total, was selected for further electrical and mechanical studies. Cleanliness is of vital importance for polymers for electrical insulation systems. The materials had a relatively large scatter in AC breakdown stress indicating a significant content of contaminants. Typically the chemical composition suggested that the contaminants in the granules could be residuals from the Ziegler-Natta catalyst and carrier particles used in the manufacturing process of polypropylene. Model cables produced from sPP granules subjected to optical pellet control had very high AC breakdown stress values compared to that obtained for a conventional homo-polymer XLPE cable system (~ 100 kV/mm at the conductor screen).
In order to make materials less vulnerable to humidity in wet service conditions, nano-particles were added to commonly used epoxy materials for subsea high voltage apparatus. It was found that nano-fillers generally had a catalysing effect on curing rate and time of the material. Although the initial results were promising, the nanoparticles tended to agglomerate themselves, sometimes reducing both electrical and mechanical properties of the insulation materials.
A method was developed to determine the dielectric loss tangent using model cables at high hydrostatic pressure and temperatures up to 130 °C in wet and dry conditions. Generally it was observed that the loss tangent was significant lower in sPP than in XLPE. At power frequency no change was observed from values obtained at ambient and dry conditions to that measured in wet and dry conditions at 130 °C. Significant higher values were observed for rubber insulated cables (EPDM), especially in wet conditions.
Ageing of insulation materials were performed to study the material degradation caused by high pressure and temperature. A special set-up was also made to study ageing caused by partial discharges at increased pressure. Different grades of polypropylene (PP) materials were aged in dry or wet high temperature conditions. The results show that the most severe ageing occurs for the samples in water vapour at 110 °C, and only minor ageing for the samples subjected to the same but dry conditions. It is believed that the water vapour likely hydrolyses the antioxidants in the sample and causes a significant acceleration of the oxidation. Ageing in liquid water was less detrimental to the samples. Ageing in nitrogen conditions caused more oxidation than in hydrostatic conditions, indicating that the pressure medium has a significant impact on the ageing rate.
In service, subsea cables are generally subjected to hydrostatic pressures and not gas pressures. Water treeing at very high hydrostatic pressures has rarely been examined, and a study was made to observe treeing in XLPE model cables at high pressures using both hydrostatic and nitrogen gas pressure. The ageing was characterized by breakdown voltage testing, water tree and SEM analysis. The results show that both ambient and high pressure conditions reduce the AC breakdown voltage of the cables significantly. The high pressure deforms voids present in miniature cables, making the density of water trees to be low. Only bow-tie water trees were observed in the XLPE insulation. Higher density of and longer bow-tie trees can be observed for the wet aged cables subjected to gas pressure compared to hydrostatic pressure.
Several test methods have been improved and adapted for high pressures up to 500 Bar.
Dielectric spectroscopy is used to determine the complex permittivity of an insulation material, from which one can derive the DC conductivity and the dielectric loss factor. With this set-up model cables can be energized up to 20 kV in the frequency range 10 mHz to 100 Hz. Test results for XLPE and sPP cables show that the dielectric loss at power frequency is low and does not have any significant temperature or voltage dependence up to 130 °C and 10-20 kV/mm. Dielectric loss in the low frequency regime is mainly due to DC conduction for both insulations.
Pd localization is a test method often used to determine fault sites in cables. The technique is based on the detection of voltage pulses originating from partial discharges in the cable. By measuring the time distance between the arrivals of voltage pulses at two different sensor positions it is possible to accurately locate the pd source. This method has been proven to be much more reliable than ordinary time domain reflectometry (TDR), as the latter method suffers from high signal attenuation in a cable. The current transformer sensor has been further developed to operate on MV power cables in sea-water at high hydrostatic pressure.
A new surface partial discharge (PD) test method was developed for high pressures, based on existing test standards. Experiments showed that the surrounding atmosphere is important for deterioration of insulation materials exposed to surface discharges. Material testing at atmospheric pressure show that 2 mm thick material samples will withstand breakdown for more than one year, with a continuous surface PD exposure in the range of 10 nC. By increasing the pressure from 1 to 4 bar the typical time to breakdown can be reduced to 24 hours. The experiments show that POM was less resistant to PD than XLPE, with initiation of degradation even after a few days ageing time. It is likely that acids are formed by the discharges catalysing the degradation of POM.
Electrical tree growth was studied at high hydrostatic pressure, using transparent silicon joints with artificial defects (sharp steel needles) in the insulation. Light emission from the partial discharges and shadow graphic images of the developing electrical tree structure was recorded in a pressure vessel with optical windows. The experiments successfully demonstrated that increased hydrostatic pressure suppresses initiation of electrical trees and breakdown in an elastomeric insulation material. At the highest pressures the silicon joints were more vulnerable to interfacial breakdown than electrical tree inception, thus material interfaces in combined insulation systems need special attention when designing high voltage components.
The subsea laboratory is considered as the main delivery from the project.
The laboratory special in its kind as it enables testing of materials and components with combined high pressure, high temperature and high voltage, with limits 500 bar, 200 °C and 100 kV. The subsea laboratory has since the initiation of the project been continuously improved to meet new challenges from manufacturers and end users of subsea equipment. Today there are more than 30 operative vessels in the subsea laboratory, covering a wide range of volumes up to 1000 litres. One pressure vessel has optical windows that enable visual observations of the test object during the experiments. Experiments with gaseous pressure or hazardous chemicals are performed at Ex-certified laboratory cells that are a special part of the subsea laboratory. A compact high voltage penetrator was developed in the project to fit the specific needs of the subsea laboratory. The penetrator design is based on a miniature model cable as the high voltage insulation component. The penetrator design is very simple, and the manufacturing time is short. Combined with a low material cost, new penetrators are always produced for new experiments. Special versions of the penetrator have been made for operation in pressure vessels with methane and gas condensate. The miniature cable penetrator has been qualified for pressures up to 515 bar and temperatures up to 140 °C. The penetrators are pd-free up to 25 kV using oil-filled cable terminations, and the breakdown voltage is higher than 45 kV. The design can readily be scaled for higher pressures, temperatures, currents, and voltage levels.