CEMCAP
WP12 Calcium looping (CaL) capture
In WP12 CO2 capture using the calcium looping (CaL) process as well as the integration of the calcium looping process into a cement plant is investigated by a consortium of three research partners: Politecnico di Milano, CSIC and University of Stuttgart (IFK). The research partners are supported by the cement manufacturer Italcementi and IKN as equipment and engineering suppliers for the cement industry.
The calcium looping process is a promising post-combustion CO2 capture technology, which is based on the cyclic calcination and carbonation of the sorbent limestone (CaCO3 ⇌ CaO + CO2). Limestone (mainly CaCO3) is calcined to CaO in an oxyfuel fired calciner at temperatures around 900°C and transferred to a carbonator which operates at temperatures around 650°C. In the carbonator the calcined CaO binds CO2 from flue gases from the rotary cement kiln and forms CaCO3 which is transferred to the calciner to regenerate the sorbent.
In the last 10 years, calcium looping has developed from a paper concept to pilot scale. It has been shown that calcium looping is an efficient and comparatively cost-effective technology for post-combustion CO2 capture in the power plant sector. Furthermore, synergies between calcium looping and cement plants have been identified. In the framework of the CEMCAP project, WP12 will identify and experimentally test key reactors for the most beneficial integration of the calcium looping process into cement plants. For this purpose process integration methods will be developed, investigated and evaluated from the techno-economic point of view in close cooperation with the industrial partners.
The overall aim of WP12 is to demonstrate calcium looping for cement plant applications in an industrially relevant environment. This will be done within long-term experimental campaigns under cement specific conditions at the 200 kW pilot plant of IFK, University of Stuttgart. The required screening for raw meals/CaL sorbents, suitable particle size distributions and a wide range of process parameters and operating conditions reflecting the cement application will be conducted by CSIC using their 30 kW CFB-CFB test rig and associated sorbent characterisation infrastructure (TGAs, SEM, XRD, etc.). Based on these experimental results, Politecnico di Milano will develop new and enhanced calcium looping process models for the simulation of a full-scale calcium looping system for cement plants.
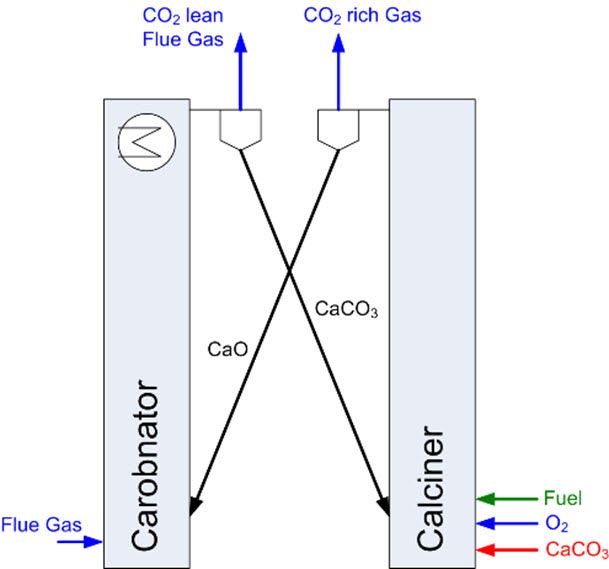