The research and industry partners already have a long tradition for collaboration and continuous innovation. The Norwegian Metal production industries are today the cleanest and most energy- and resource efficient in the world, with emissions of greenhouse gases (GHG) reduced by almost 40 % in the last 20 years, without reducing the total production volume.
SFI Metal Production is a program under the Research Council of Norway (RCN). The Centre has a total budget of 256 mill NOK over eight years with contributions from the industry, RCN and the Research Partners.
SFI Metal Production is:
- Developing new knowledge on existing and future processes for the production of metals.
The chemical reaction rate in production of manganese-alloys containing silicon (SiMn) is dependent on trace elements such as sulphur in the raw material. It is also established that the reaction rate of silicon containing manganese alloys is much more dependent on temperature in the reaction zone than comparable alloys without silicon (FeMn). Methods have also been developed to evaluate the quality in sampling of mixed metal-slag systems. This will contribute to improved control of the metal quality. The dissolution of alumina is a key parameter in determining the performance of primary aluminium production and also linked to emissions of greenhouse gases. The development of new knowledge and models for alumina dissolution is an essential topic in the Centre. -
Contributing to better utilisation of resources and increased recycling of materials.
Recycling of packaging material based on aluminium is studied in the centre, with strong involvement of students, the metal producing industry and companies that have a responsibility for used packaging on the Norwegian market. SFI Metal Production has a focus on the understanding of parameters such as the effect of food residue and plastics on the quality and metal yield in recycling. The Centre has also contributed with knowledge to reduce future metal loss by oxidation from the handling of liquid aluminium. New insights into the oxidation mechanisms of liquid aluminium alloys can contribute to replace beryllium in the future as an agent to reduce oxidation loss. -
Educating highly skilled metallurgical engineers and scientists for the industry and academia.
SFI Metal Production has all categories of students - from Bachelor, Master (ca 10 per year) and PhD. A total of 14 PhD and 5 Post Doc are planned in the centre of whom eight PhD already has started their study. All PhD students have their own resource-group with 2-3 representatives from the industry. This arrangement will ensure excellent contact between industry and the PhD students. In addition, this will contribute to a professional foundation in the industry. -
Contributing to keep the Norwegian industry as a world leader of sustainable metal production.
One example is PAH (polycyclic aromatic hydrocarbons) that can be detected in very low concentrations in the off-gases from the production of ferroalloys and aluminium. In SFI Metal Production, a more reliable system for measuring PAH in low concentrations has been developed. The centre has also contributed to an improved understanding of fugitive emission from industry that can serve as a basis for working environment actions.
SFI Metal Production will contribute to:
-
Sustainable innovation: Ensure that the Norwegian Industry has optimal conditions to develop new sustainable products and more environmental and energy- and cost-effective production processes.
-
Industrial growth: Basis for faster implementation of technological breakthrough to create competitive advantages as a basis for growth and new companies.
Centre Partners: Host institution NTNU together with the Research Partners SINTEF Industry, SINTEF Energy and Teknova. Industry partners: Hydro, Alcoa, Elkem, Eramet Norway, Finnfjord, FerroGlobe Manganese Norway, Wacker Chemicals Norway, TiZir Titanium & Iron and GE.
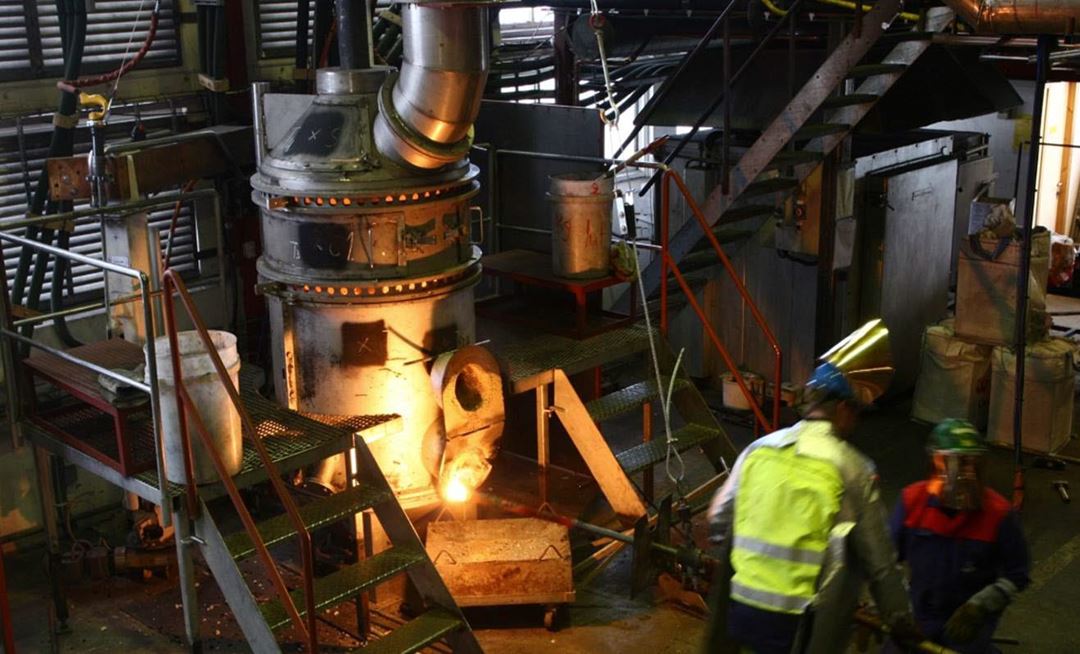