Recurring maintenance is necessary in many industries (e.g. power grids, buildings, ships and airplanes). In the railway domain the vehicles (e.g. locomotives, freight cars and passenger cars) are taken out of their revenue-generating service (transporting goods or passengers) and moved to a maintenance depot. There, maintenance activities are performed before the vehicles are returned to service. Planned maintenance tasks (similar to a car's 10.000-kilometre service) have substantial fixed costs in terms of staff, equipment and vehicle transportation. Therefore, it is very important to perform as many of the maintenance tasks as possible when a vehicle is undergoing planned maintenance. At the same time, we are required to have enough resources available to cover unplanned urgent maintenance.
Currently, maintenance planning in railways is predominantly done manually and involves solving the following connected planning problems (see figure): crew scheduling (assigning maintenance tasks to crews dependent on skill sets): job shop scheduling (assigning time slots for vehicles at certain depot workstations). Optimally, these activities should be synchronised with vehicles' revenue-generating activity (vehicle owners commitment to transporting goods and passengers).
Individually, these planning problems are very complex due to the sheer number of tasks and resources involved. Because of this complexity, manually finding solutions is not only time-consuming but highly inefficient both for the maintenance companies and their customers, and inefficient solutions are costly. Due to the substantial fixed costs involved, inefficient solutions are very costly. Few tools exist that help to generate maintenance plans, and they normally focus on myopic parts of the overall problem (e.g. they exclude crew planning or have fewer parameters). Existing approaches try to solve the planning problems independently and then merge the plans, thereby losing the global perspective necessary to achieve the required efficiency. Individually, these planning problems have been studied at length in the scientific literature and in other industries, optimisation-based planning tools are used frequently. For example, optimisation-based planning tools for airplane and ship maintenance have been applied successfully for decades. Perhaps due to the fact that railway-related industries are mostly government-owned and lack competition, maintenance planning has been met not with efficiency but complacency. We believe it is time to catch up and learn from other industries by applying optimisation techniques to increase efficiency in railway maintenance.
This project will give us (Mantena) the much needed resources to invest in research from SINTEF Optimisation, who will create an optimisation-based maintenance planning tool, that can solve these interconnected planning problems simultaneously while respecting the shared and limited resources. This innovative optimisation engine will drastically reduce the costs related to maintenance. This will be partly due to our crew being better scheduled, such that less overtime will be necessary and we can give them more attractive working hours. In addition, this project will also allow us to order maintenance tasks more efficiently such that more it will also be able to perform the maintenance in a more efficient order, such that more tasks can be performed during the same time span. To our customers in the project (NSB, Flytoget and CargoNet), this planning tool will not only result in reduced costs but also more reliable and efficient service that will minimise the time that each vehicle is removed from revenue-generating service. In addition, this planning tool will enable more maintenance to be performed during seasonal off-peak periods, when railway vehicles are used less often. In this way, we may even reduce the total number of vehicles our customers need to fulfil their commitments, which is a major cost saving. Altogether, these efforts will give us a significant competitive advantage over our competitors.
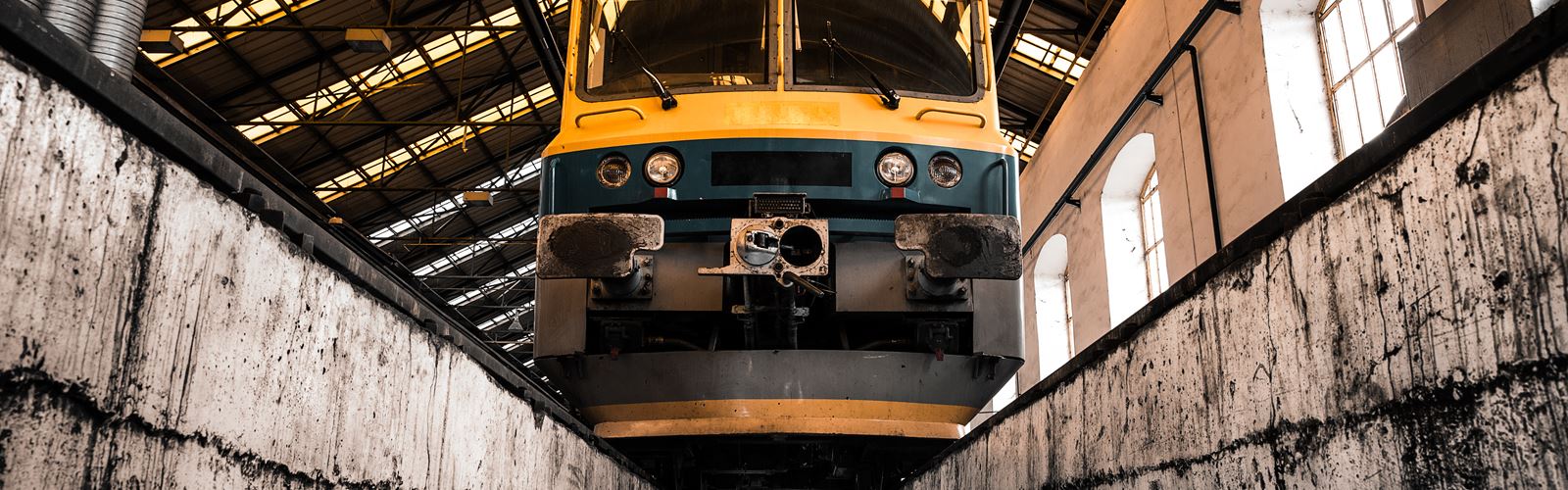
MainMan
Currently, maintenance planning in the railroad domain is predominantly performed manually and involves: Crew scheduling (assigning maintenance tasks to crews dependent on skill set) and job shop scheduling (assign time slots for vehicles to depot workstations).
These activities should be synchronised and coordinated with vehicles revenue generating activity (where the vehicles are scheduled to transporting goods or passengers).
Due to the substantial fixed costs involved, improved planning is expected to generate significant cost savings.
Contact person
Key facts
Project duration
2017 - 2021