Inspection and repair of aquaculture nets in fish farms are both resource- and time-intensive. While remotely operated underwater vehicles (ROVs) are increasingly used for inspection operations, current solutions do not fully exploit the potential of these vehicles. Inspections are typically conducted by an ROV operator who remotely controls the robot while monitoring video footage of the net to manually detect damages and holes.
Even with skilled and experienced operators, this is a challenging task, and small holes or damages can easily be overlooked. Minor holes detected during inspections are repaired by diver teams, but this is resource-demanding and may cause delays between detection and repair. Additionally, diving operations always involve a degree of risk, even when strict safety protocols are followed.
Through the AquaStar project, we aim to improve net inspection using underwater vehicles by making them more autonomous and robust, with features such as automatic hole detection and autonomous navigation relative to the net, holes, and other areas of interest.
In addition, we aim to enable temporary hole repair by equipping the underwater robot with a robotic arm (manipulator), implementing a control system for the combined vehicle-manipulator system, and developing a dedicated repair tool for hole patching. This will free up resources, reduce costs, and lower the risk of fish escaping through improved accuracy and more frequent inspection operations.
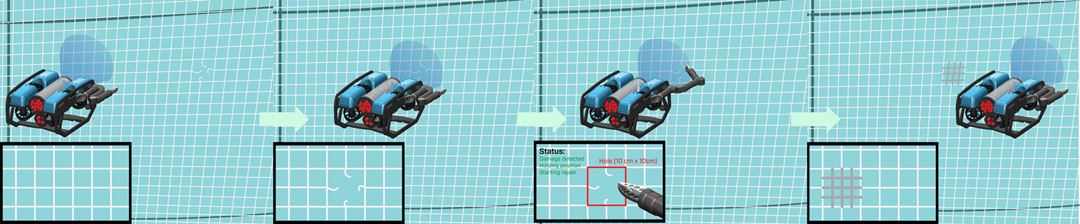
The results will be validated through laboratory and field experiments to ensure the solutions are applicable in operational facilities. By promoting automation and innovative technological solutions, AquaStar will help make the aquaculture industry more sustainable and future oriented. Furthermore, the technology developed will also be applicable to other marine industries where vehicle-manipulator systems are used.