A green transition to less carbon emissions still requires construction and utilization of chalk and paper in general. Common materials used all around us are cement, paper and chalk. These materials have one thing in common, they require high temperature processing of their raw materials, while cement, with calcination and clinkering is the most demanding. Nevertheless, its unique properties make it the foundation of the construction industry.
The production of cement is directly linked to massive amounts of Green House Gass (GHG) Emissions, explicitly CO2, released during the calcination and clinkering of the raw meal. The calcination itself is an intermediate temperature process (around 900C), releasing chemically bond CO2 from calcium carbonate (CaCO3) to calcium oxide (CaO), where the raw materials are lime and limestone. This process can be electrified by resistive heating elements, utilizing the process heat from the kiln or a combination of both.
- CaCO3 → CaO + CO2
A high purity CO2 stream can be generated, simplifying the carbon capture and storage (CCS)
During the clinkering reaction, the CaO reacts with silica, alumina and Fe2O3 to different clinker minerals, e.g. alite and belite.
- 2CaO + SiO2 → 2CaO*SiO2(C2S) (at the range of 900 to 1300C)
- 2CaO*SiO2 + CaO → 3CaO*SiO2(C3S) (at a range of 1300 to 1450C)
This reaction requires elevated temperatures (<1300C), that are not achievable by resistive heating and require alternative solutions, which are capable of industrial scaling, giving power ratings in MW to GW and robust in implementation.
In Electra we will work on the electrification of both; 1. the clinkering process by investigating alternative burners for rotating kiln applications and 2. alternative calcination processes, such as fluidized bed reactors and electrical heated gas streams.
The implementation of two different state-of-the-art thermal plasma torches are the promising candidates for replacing the fossil fuel burners. SINTEF’s contribution is the work with one of these plasma torches, as one has been developed in-house at the SINTEF MPP group and recently has succeeded with a patent application in 11.2024. This plasma torch is unique and especially suited for the required environment, temperature and industrial complexity. Nevertheless, these torches are new to this environment and require testing and validation, which go together with the modifications and adjustments to the industrial reactors / kilns, where these are to be implemented. In addition, SINTEF is going to use the in-house designed plasma torch testing reactor for further developing thermal plasma technology. As the final task, SINTEF is building and piloting an industrial scale rotating kiln for calcination and clinkering of raw materials for up to 0.5 tons/h using the in house developed plasma torch.
The electrification would remove the CO2 from the fuel and reduce the combustion of fossil fuels for the clinkering process. This also increases the CO2 part in the else smaller off gas stream, making it easier for CCS and CCU. And the best part of the new plasma torches is, that they use CO2 as fuel, producing the same amount of CO2 as you put in, e.g. releasing only thermal energy to the process.
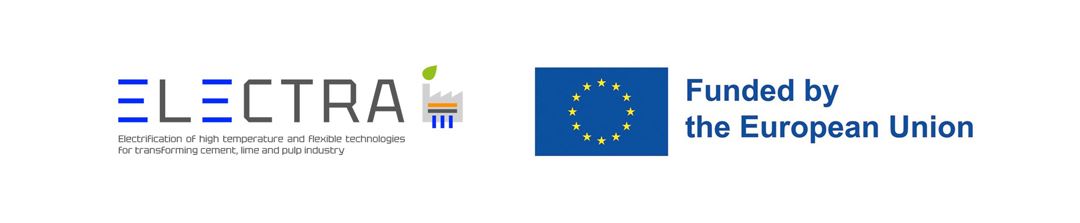