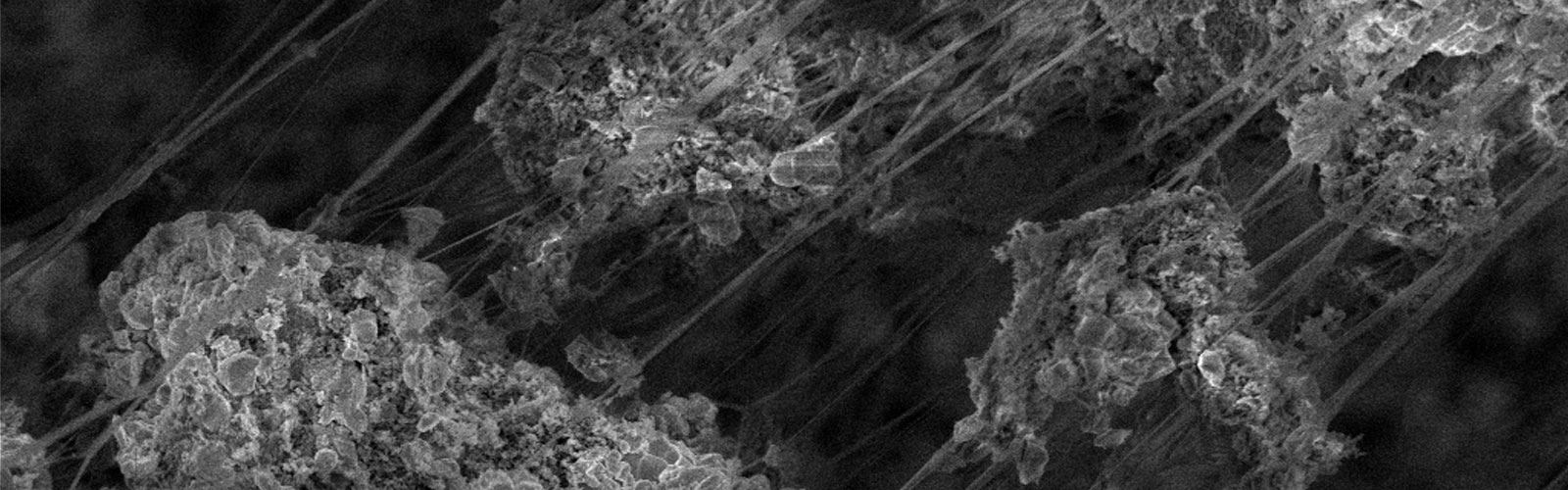
UltraDry – Unlocking the potential of sustainable and solvent-free fabrication of electrodes for Li-ion battery cells
Background
In what way can the production process of Li-ion batteries be improved? And why is it important?
Batteries play a key role in the green transition to solve the global climate crisis, for example by enabling zero-emission transport (e.g. electric vehicles and ferries) and by storing the energy from intermittent renewable sources. The global demand for batteries is expected to skyrocket the next 10 years, which raises the necessity for the corresponding increase in battery production to be as sustainable as possible.
Battery electrodes are typically made by mixing the battery materials in a solvent and casting a thin layer of this wet slurry on a metal foil current collector. Before the electrode layers can be assembled into a working battery, however, it is critical that all of the solvents are removed so that the electrodes are completely dry. This drying process is expensive because it requires a lot of energy to power the drying ovens that are tens of meters long. Also, the solvents that are typically used for making the cathodes are harmful and polluting, which further complicates the process and increases the cost. For the last few years, alternative solvent-free methods for making battery electrodes have gained more and more attention. This type of dry processing have proved to be quite complex and there is a lack of fundamental understanding of how the different steps in the processes interact to influence the final properties of the electrode.
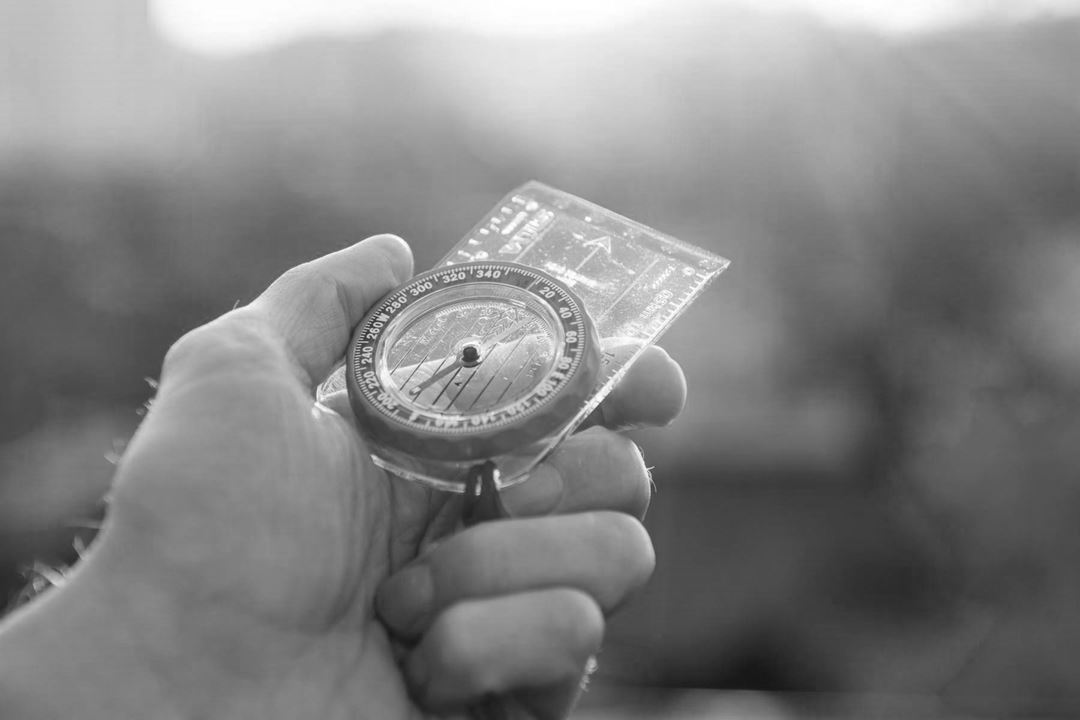
Furthermore, the polymer binders used in the battery electrodes and the salts used for raising Li-ion conduction in the battery electrolytes have a high content of the element fluorine (F). Due to environmental concerns and the potentially harmful fluorinated chemicals that can be released upon battery failure or recycling, there is a pressing need for developing more sustainable battery additives with a minimal amount of fluorine.
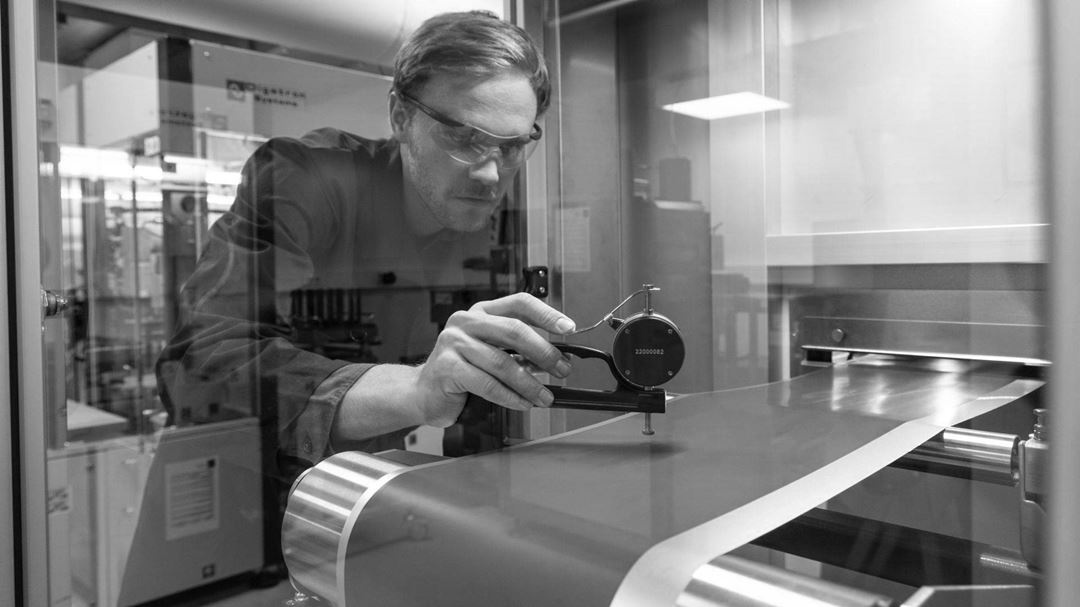