The welding process selected is a variant of the MIG process; the Fronius CMT (Cold Metal Transfer) process, which is extensive used in conventional thin plate and root pass welding. CMT is characterized by low spatter formation and good bridging capabilities, which are crucial factors affecting the operational robustness. The goal is to adapt the CMT process to hyperbaric conditions, i.e. under pressure corresponding to the actual sea depth. For initial experimental welding under hyperbaric conditions a special designed 35 bar chamber is built and installed at SINTEF. The chamber can be rotated allowing welding in different fixed positions, simulating orbital pipe welding. Verification experiments under pressure up to 150 bar, corresponding to 1500 meter sea depth, will be performed at Statoils hyperbaric welding laboratory in Haugesund.
The first part of the work has been testing and modification of process parameters in bead on plate welding with the objective to achieve a stable process under ambient argon pressure up to 35 bar. Initial root pass welding trials have been carried out. An example of a root pass welded with 2mm root opening in the 6 o'clock (overhead) position is shown in the figure below. Here an Alloy 59 welding wire is used. Different types of wires will however be evaluated with respect to process and weld metal properties both for welding C-Mn and clad pipe steels.
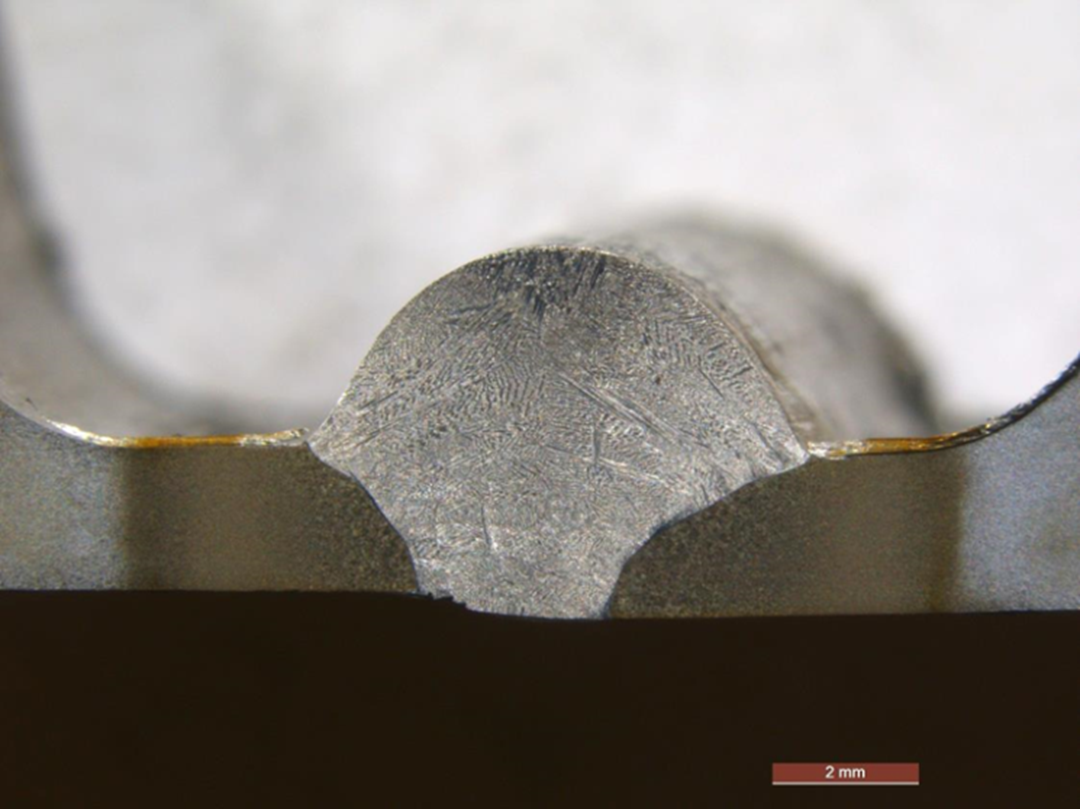
The CMT process is characterized by low heat input which is advantageous for handling the root welding. However, for the filler passes higher heat input and deeper penetration are needed to avoid lack of fusion. Hence, after the CMT root pass welding is acceptable, process mode and parameters for the selected wire giving higher heat input, will be prioritized .
In the end of the project complete welding procedures for X65, clad and high Mn steels will be developed and qualified. Cooling rates at different ambient pressures will be measured and given as input to the weld modelling work.