Welding procedures are often established by trial-and-error to achieve acceptable welds. Industries are often very conservative with regards to applying the numerical modelling for welding due to the lack of efficient tools as well as cost considerations. With the rapid increase of computational capacity and better understanding of welding physics, numerical modelling of welding has become more and more relevant for optimization of welding parameters and improvement of the quality of welded structures.
In the ROP project, weld modelling will be used for optimization of welding parameters at high pressures where the deposition of the root pass is an important challenge. Due to the complex situation in weld repair of clad or lined pipes, with three different materials in the joint, simple simulations will be very helpful to avoid formation of phases that may be harmful to the joint properties with subsequent risk of cracking. In-deep understanding of the effect of pressure on the arc physics, flow and mass transfer inside the weld molten pool and global thermo-mechanical behavior is needed to achieve robust weld joints.
So-called "through-process modelling" approach will be applied to optimize the welding process and avoid formation of phases that may be harmful to the joint properties with subsequent risk of cracking.
Numerical tools that will be used in through-process modelling are described as following:
• Weld arc modelling (COMSOL Multiphysics®) will involve the computation of the temperature and current density in the welding arc with focus on the effect of pressure and shield gas composition. This will provide realistic boundary conditions for the weld molten pool modelling.
• Molten pool flow modelling (SWIM-FLOW) will investigate the local flow behaviour and mass transfer inside the weld pool. This will closely link arc modelling and weld joint property prediction. The results from arc modelling will give valuable input for molten pool modelling, and the output will supply important information for global thermal-mechanical simulation, e.g., weld bead profile.
• Joint property modelling (WeldSimS) will focus on the materials' response to welding includes the computation of heat transfer, phase transformations, residual stresses and hydrogen diffusion. The results from arc and molten pool modelling will be exploited by imposing the weld pool shape and the dilution of weld and base metal computed in the more detailed local model. This will give better input for analysis of structural performance, e.g., hydrogen embrittlement.
• Structural performance analysis (ABAQUS) will mainly study hydrogen induced and/or assisted embrittlement and the risk of ductile or brittle fracture. The effect of residual stresses may be important since they may influence the HE resistance as well as ductile or brittle fracture. Distribution of residual stresses and hydrogen diffusion from joint property modelling will supply good basis for such analysis.
In summary, through-process modelling of hyperbaric welding is expected to obtain better understanding of the relationships between process, property and performance (3Ps) of hyperbaric welded structures. Modelling these stages as an integral system can thus transform the hyperbaric welding process development from an "empirical-based" to a "physical-based" process.
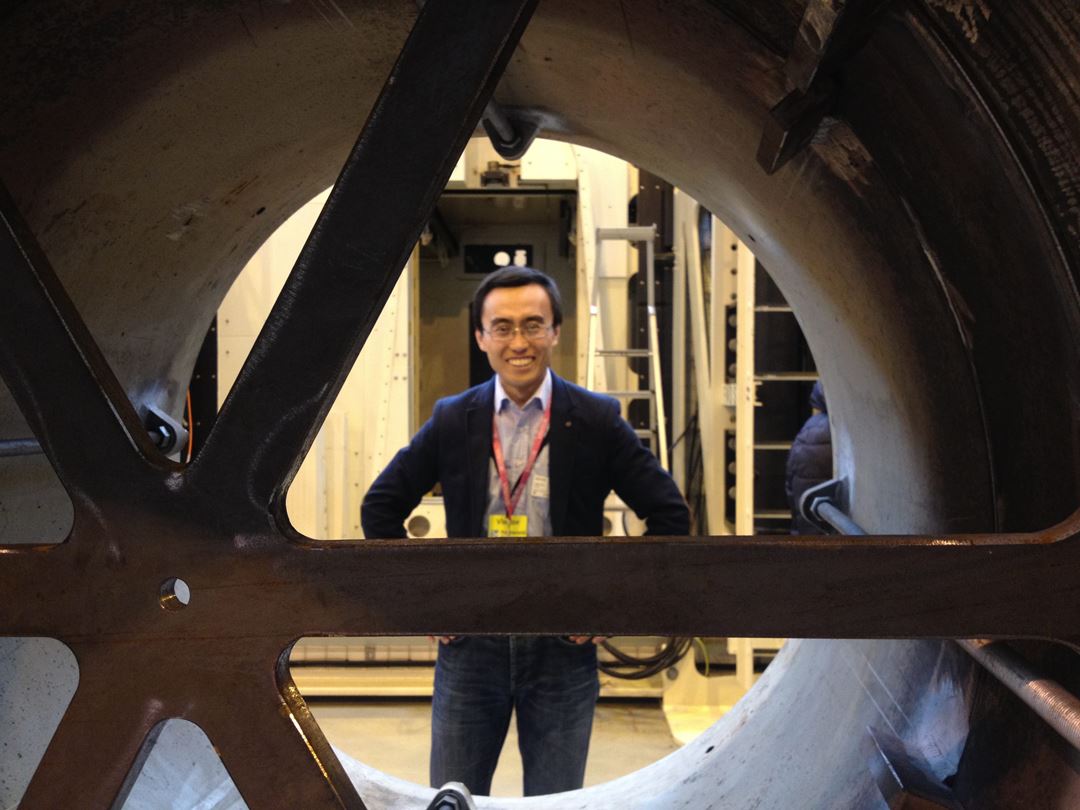
Contacts
• Xiaobo Ren, SINTEF Materials and Chemistry
• Vigdis Olden, SINTEF Materials and Chemistry
• Hallvard Fjær, IFE, Institute for Energy Technology
• Dag Lindholm, IFE, Institute for Energy Technology
• Magne Rudshaug, IFE, Institute for Energy Technology