The challenge
Structural materials will inherently have cracks and defects. Steel structures like pipelines are subject to extreme loading conditions, thus defects may grow during installation and operation.
Erosion, corrosion, fatigue and other degradation mechanisms may also introduce new defects over years of operation.
During the design phase allowable defect sizes that ensure safe installation and operation over the lifetime of the pipeline is determined.
Design rules based on analytical relationships, although representing the extraction of experience and theoretical knowledge collected over generations, may be lacking in accuracy and lead to non-conservative or inefficient designs.
More accurate design tools are important to help safeguard human, environmental and economic resources. Advanced computer models, normally in the form of 3D finite element (FE) analyses, are utilized to improve the design – safe designs, with optimized margins within the design rules are the result. However, these advanced computer models, until today, have been tedious, complicated and time consuming in use and thus impractical for design purposes.
The solution
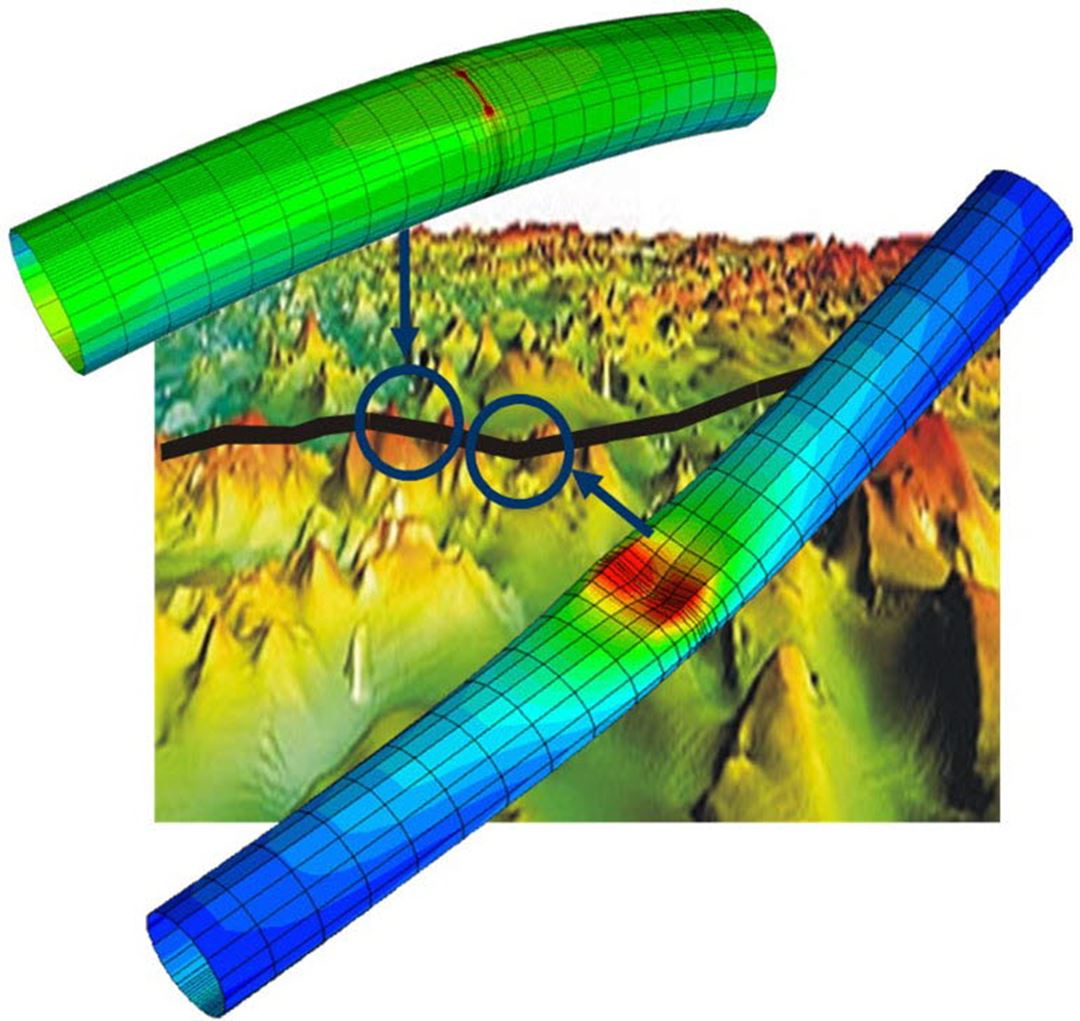
LINKpipe is a non-linear, special-purpose finite element tool for performing fatigue and fracture mechanics calculations in pipelines and piping structures.
The LINKpipe tool offers a strong improvement in pipeline design technology. Fracture mechanics theory and practice has, through the LINKpipe software been merged with the finite element models of the design engineers – effectively merging the expertise of the pipeline design engineer with that of the materials and fracture mechanics experts.
LINKpipe implements the most advanced technology in the field, including the most recent state-of-the-art advances within strain-based fracture assessment, developed by a group of experts at the Norwegian University of Science and Technology (NTNU) and SINTEF. LINKpipe is a commercially available software program offered by SINTEF.
LINKpipe = A Shell element model + the improved linespring element
LINKpipe tells you which cracks are critical
Monitoring and inspection data offer information on the location and size of defects. LINKpipe provides you with a conclusion:
- As to whether you may safely continue the operation, or
- If a repair/replacement is required
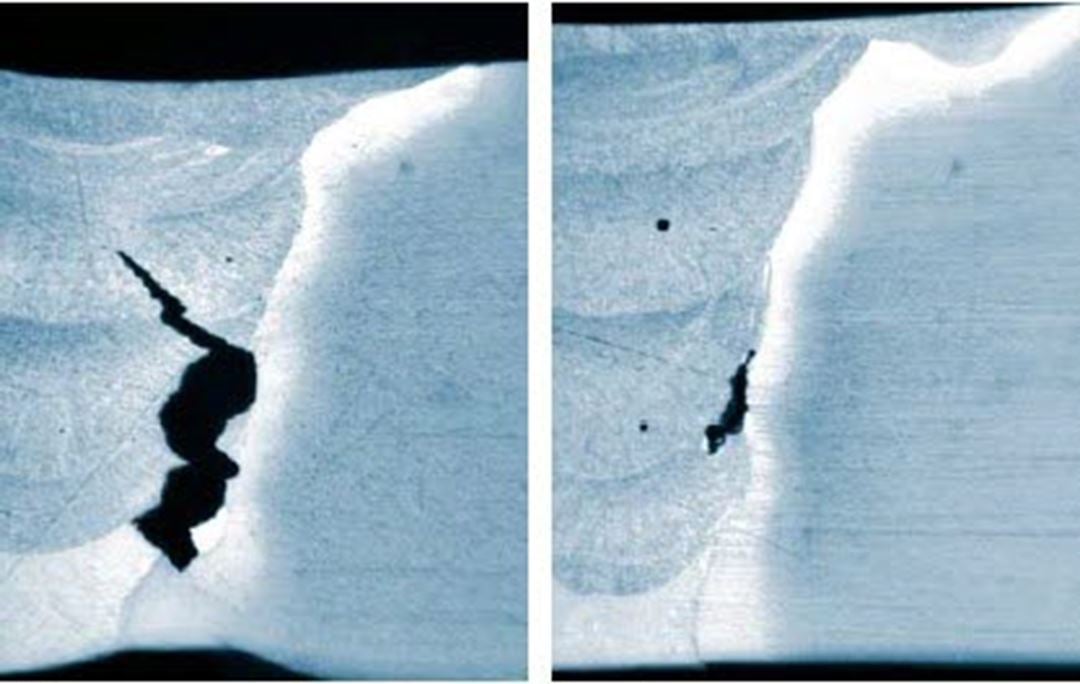
LINKpipe can be used for:
- Pipeline installation
- S-lay, J-lay and Reeling
- J-tube pull-in
- Subsea pipeline operations
- Lateral buckling, upheaval buckling, free spans
- Shut-ins/shutdowns (pressure and temperature cycling)
- Operation outside of design envelope
- Arctic pipeline design
- Frost heave and thaw settlement
- Ice gouging/sub-gouge deformation
- Pipelines subjected to large ground displacements
- Seismic loading
- Lateral spreading (loss of stability/slides)
- Fracture and/or bulking of pipelines subjected to corrosion
- Effects on integrity from loss of wall thickness
- Fatigue assessment to crack-like defects
- Early pipeline design
- Sensitivity studies
- Specification of required material resistance
- Tendons, umbilical, general tubular structures
- Accidental loading scenarios
- Anchor hooking