- Name
- Brage Rugstad Knudsen
- Title
- Leader RA 6 Case Studies
- Organization
Case Studies RA6

Case Studies were performed to promote HighEFF innovations and obtain measurable results from the implementation of HighEFF technologies in the different industrial sectors. The Final results section below gives an overview of results for our main case studies.
Final results
Investigations on potential uses of CO
We investigated various innovative uses of industrial off-gases such as carbon dioxide and in particular carbon monoxide. The interest in utilising these gases has grown over the lifetime of the Centre, along with general climate awareness. The low-hanging fruit is to use the off-gas as a source of energy, both directly and indirectly. It can be argued that CO-rich off gas has greater value as a source of chemicals than as a source of energy. One of our key areas of focus has thus been to explore novel applications beyond traditional uses like fuel burning or energy recovery, including novel low-TRL opportunities.
As a chemical agent, the main use of CO gas internally in ferromanganese plants would be for pre-reduction of ores, a topic that has received a lot of attention lately, see for example in RA4's Final results section.
When mixed with hydrogen, CO forms syngas, the building block for a lot of organic chemistry. We have discussed how methanol could be produced from offgas. While market competitiveness will be challenging, projects on ship fuel show some promise as ore and metal are typically transported by boat. CO can also be used in the production of hydrogen, through water gasshift reactions. In the first iteration of this work, we explored how such a project could power local fleets of hydrogen buses, by using overall CO₂-emissions to generate hydrogen. In the second iteration, only a few years later, the idea of producing hydrogen with CO₂-emissions seemed almost quaint, an example of how quickly the sentiments surrounding CO₂-emissions and emissions targets have changed over the lifetime of the Centre. The example also served to highlight the regulatory challenges surrounding the use of off-gases and determining how to count emissions and emissions-savings. Thus, a final action was to dig into the EU-taxonomy and how it relates to this matter.
Finding novel uses for surplus heat
Initial work revealed a promising potential for using low-grade heat from energy intensive industry externally in the production of food and other biomass. We performed case studies to investigate selected heat users that could be established in conjunction with existing heat producers.
Metal producers have been studied as the primary surplus heat producers, but we believe findings are transferable to upcoming industries such as battery manufacturers and data centres. The case studies were focused on four types of heat users: Greenhouses, fish farming, insect rearing, and seaweed drying. Successful examples of the first two exist today, but a large upscaling potential in terms of energy recovery rate and sustainable food production was highlighted. Our studies of the latter two were more conceptual, motivated by possible reductions in protein import for the first one and a growing demand for biomass for the last one.
A novel concept for a surplus heat-driven industry cluster combining these actors was also developed and published, combining complementary heat demands and synergistic material streams. Lastly, to help facilitate the upscaling of a novel seaweed farming industry, we performed techno-economic evaluations of a seaweed value chain using surplus heat for drying close to potential farming areas.
Advancing energy efficiency in food industries
Comprehensive R&D efforts have been carried out to push forward innovation and and the implementation of energy efficiency measures in the food industry. In some processes, a possible reduction of up to 75% in primary energy use was identified by using already existing excess heat from the plant as well as integrating heat pumps that can deliver cooling and heating at the same time. The availability of surplus heat and the predominance of process heat requirements below 200°C make the food sector a prime candidate for deploying high-temperature heat pumps to reduce and ultimately eliminate use of fossil fuel-based heating in these industries.
Reducing emissions from gas processing plants
Conversion from natural gas to hydrogen
With hydrogen expected to be available at the Gassco Kollsnes plant by the end of the decade, replacing natural gas with hydrogen – either fully or partially – in the plant’s three gas-fired oil-heating furnaces is under consideration. A CFD study examined the impact of this fuel switch focusing on heat loss to the furnace walls and its effect on heat transfer to the oil. The results of this study reveal no showstoppers in terms of converting from natural gas to hydrogen. For the three furnaces at Kollsnes, a significant reduction in CO₂ emissions from the furnaces could be achieved. Depending on the thermal input, the estimated reduction was between 38,500 and 58,500 tons of CO₂/year, assuming an operating time of 8,000 hours/year.
2023 Results
CO-rich off-gas
A previous, technology-focused case study on utilisation of CO-rich off-gas from manganese ferroalloy production has been complemented by an overview of how EU regulations are impacting the techno-economic evaluation of the different utilisation options. Various regulatory frameworks are covered, including the taxonomy for sustainable activities, the corporate sustainability reporting directive, the industrial emissions directive, and the emission trade system (ETS). The report focuses on how the new or updated regulations and directives may influence the investment decisions for ferroalloy producers. The ETS's allocation methods for free emission allowances and how the ETS interacts with the upcoming, new carbon border adjustment mechanism (CBAM) for ferroalloy producers seem to be particularly impactful.
Industrial Energy Communities
Several industrial actors are aiming to electrify their processes but are frequently met with the challenge of limited capacity in the electricity grid. In the literature, energy communities are typically investigated as a means to incentivise efficient resource utilisation, e.g. to reduce electricity peak demands. The research on energy communities has so far mainly focused on households, electric vehicle charging, and to some degree commercial building such as offices. In this work, we have investigated the potential for integrating an industrial actor – more specifically a dairy – into an energy community. We investigate how energy storage can enable reduced loads in the dairy, thereby lowering the grid tariffs, which are typically driven by the peak electricity demand within a given month. We compare the cases of a thermal energy storage optimised for the industrial actor, to a case where the storage is used for reducing the peak demand of the entire area. We find that thermal energy storage is favourable compared to a battery, and that the energy storage may potentially contribute to 1 MW of increased grid capacity for the area, at the same time as it reduces costs both for the industry actor and the area.
Energy efficiency potential of retrofit projects in fish processing plants
Conversion of Kollsnes furnaces from natural gas to hydrogen
At the Gassco Kollsnes gas processing plant, three gas-fired furnaces are used to heat oil. Reducing the CO₂ emissions from the furnaces is an objective. As hydrogen is expected to be available at the Kollsnes plant by the end of the decade, full or partial replacement of natural gas with hydrogen is of interest. The aim of this case study is to investigate the conversion of Kollsnes' furnaces from natural gas to hydrogen (or a mixture of them) to reduce CO₂ emissions. A CFD model of the Kollsnes furnace was built, and simulations with natural gas as fuel were performed and validated against data received from Gassco. Natural gas has been replaced with hydrogen in the model, and simulations are ongoing.
Cost estimation of seaweed drying
This ongoing study considers the costs of establishing and operating a cultivated seaweed value chain, from seed deployment to dried product. Techno-economic analysis methods are used to evaluate the cost of using surplus heat from the metallurgical industry sector for the processing step, in order to assess the potential of this contributing to an upscaling of production. Uncertainties related to this upscaling, as well as to geographical variations and the use of immature technology, have been integrated into the study by use of stochastic input data combined with statistical output analysis. In 2023, preliminary results were presented for typical Norwegian conditions and for a Karmøy-based case study. These estimate that the cost of using surplus heat for processing will be marginal compared the cost of cultivation, indicating this as a promising option for upscaling the value chain should energy availability become a concern. With current seaweed prices however, the production is not profitable without including carbon pricing, and thus the carbon removal potential of this value chain is also included in the study going forward.
2022 Results
Thermal energy storage technology air-conditioning for a CO₂ supermarket refrigeration system
Modern supermarket refrigeration systems are based on transcritical CO₂ booster systems, supplying cooling and freezing of the products in the store. Currently, the air-conditioning (AC) in REMA 1000 supermarkets is supplied by a glycol circuit which is cooled by the CO₂ rack. The design capacity of the rack must handle all the refrigeration load and the AC load during the warmest summer day, which results in overcapacity and part load operation for most of the year. In this case study, it is suggested to replace the glycol circuit to the air handling units by a combination of CO₂ circuit and a cold thermal energy storage. The thermal energy storage is using water/ice as the storage medium and can be used to store cold energy during the night and supply AC during the peak hours during the day. The simulation results in this study shows that the peak power load required from the electrical grid during a summer week can be reduced by 13%-19%, depending on the location. When investigating various scenarios for electricity pricing, it was found that the economic attractiveness of the technology is very sensitive to the pricing scheme and location. It is recommended to conduct a more in-depth study for a year of operation, and to investigate the possibility to establish a pilot installation to demonstrate the technology in a real supermarket. A conference paper based on this HighEFF case study has been written and accepted for presentation at the 2023 IIR Ammonia and CO₂ Refrigeration Technologies Conference.
Energy efficiency potential of retrofit projects in fish processing plants
This study builds on the work on energy efficiency measures in new fish processing plants conducted in 2021. The current case study evaluates potential energy efficiency measures for an existing fish meal and oil factory. Measurement data from a processing plant are analysed, identifying the heating demands and mapping the potential waste heat sources. The focus is on integration of high-temperature heat pumps upgrading waste heat from the factory to produce low-pressure steam for the cookers. Three waste heat sources were evaluated: condensate from the MVR evaporator, water from cooling towers and waste heat from a nearby freezing factory. In order to produce steam at 3 bar, two different heat pump solutions were considered: a closed loop steam heat pump and a butane heat pump with a steam top cycle. System solutions were considered using the different waste heat sources together. The results show a significant potential for using the waste heat sources to produce low pressure steam, particularly using the condensate from the MVR evaporator, which gave a COP of 2.3-2.7. Water from the cooling towers is likely not useful due to low temperatures.
Conversion of Kollsnes furnaces from natural gas to hydrogen
At the Gassco Kollsnes gas processing plant, three fuel gas-fired furnaces are used to heat the hot oil. Reducing the CO₂ emissions from the furnaces is an objective. As hydrogen is expected to be available at the Kollsnes plant by the end of the decade, full or partial replacement of fuel gas with hydrogen is of interest. The aim of this case study is to investigate the conversion of Kollsnes' furnaces from natural gas to hydrogen or a mixture of them to reduce CO₂ emissions. Initial CFD simulations were performed for the Kollsnes furnace.
2021 Results
Heat integration on offshore platforms
A comprehensive and generic oil and gas platform model was developed to contrast energy-efficiency measures, focusing on recovery and utilisation of surplus energy Upon validation against real data for two platforms, various scenarios where compared based on carbon footprint, energy efficiency, and operational costs (CO₂ tax and fuel cost). The use of steam bottoming cycles, H₂ blending, and wind energy were found to be the most effective configurations. Based on the most promising technologies, a lowemission scenario was developed with the use of a smaller, more efficient gas turbine with a steam bottoming cycle and wind energy during the first 15 years of operation. Subsequently, it was proposed to gradually introduce H₂ fuel, starting with 50 molar % blend up to 90 molar % Over a 30-year lifespan, the proposed low-emission scenario would reduce CO₂ emissions by up to 2 7 Mtonnes.
Energy efficiency in food processing
A case study at the Orkla’s production site at Skreia identified a large energy saving potential in the potato chip production line Preliminary results indicate that the use of high-temperature heat pumps could reduce energy consumption by up to 60% and reduce CO₂ emissions by up to 93%. This investigation represents a first phase in the study, and it is based on preliminary data received from Orkla. The considered processed data should be verified before investment costs are further evaluated.
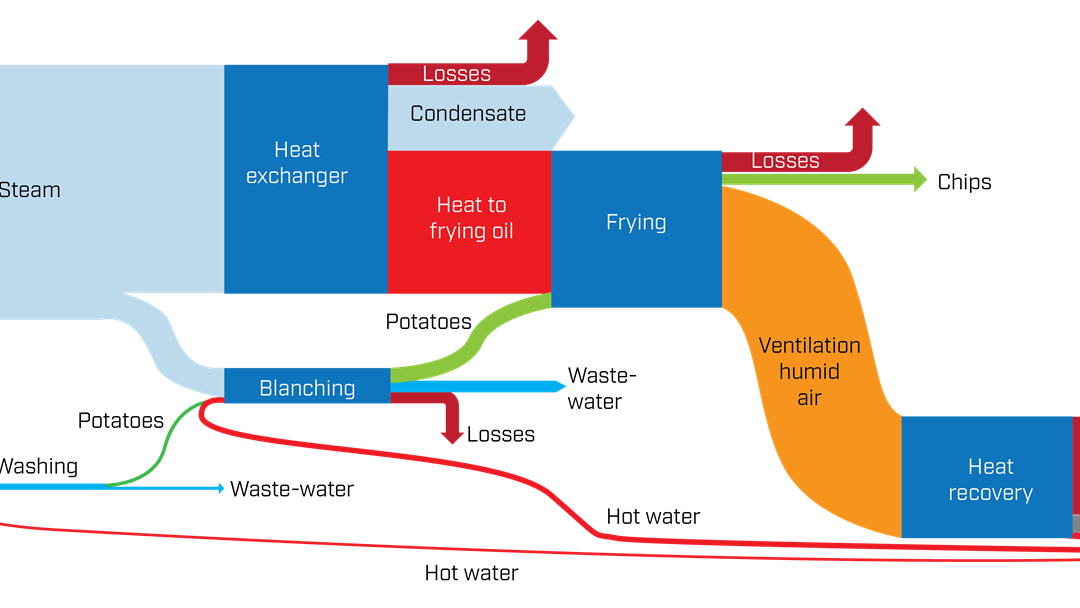
Joint mapping of metallurgical surplus heat and potential seaweed growing
The cultivation and farming of seaweed on the Norwegian Continental Shelf is a growing industry with large potential for sustainable production of biomass As the water content of the products is very high, preservation by drying is needed The drying processes used today are very energy-intensive but done at relatively low temperatures As such, this industry represents a potential use case for low-grade surplus heat. In 2021, the potential and implications of recovering this heat from the metallurgical industry has been studied, hoping to benefit from plants being situated along the coast, close to potential farming areas. Ongoing efforts at HighEFF to map available surplus heat from metal producers in Norway have been combined with maps of off shore seaweed cultivation conditions to provide an overview of the potential. Based on these mapping efforts, a case study considering heat from Hydro Karmøy was performed It was found that in a 2-month long harvesting season, 66 GWh of heat could potentially be used to dry 63 Mt of raw seaweed, corresponding to a CO₂ uptake from the atmosphere of around 5750 tons. Compared with the use of an electric boiler for seaweed drying, the use of surplus heat provides an additional CO₂ avoidance of roughly 1000 tonnes.
2020 Results
The energy savings at TINE dairy in Bergen were verified, and close to 40% energy savings were proven. The energy efficiency is still increasing and is likely to reach 50% or more when the dairy has been fine-tuned. This was achieved by integrating the heating and cooling demands at the dairy through heat pumps and thermal storage tanks. The overall energy flow over a week is presented in the figure. This is the first known dairy where all heating and cooling demands can be delivered by heat pumps, all the way from -1.5 °C to 95 °C. The results prove that the energy efficiency of industrial heating and cooling can be significantly increased by focusing on energy savings already at the design phase of new plants. The systems used are also relevant for several other industries, both in Norway and Europe, and the work has been summarised in a journal paper currently under review by peers.
We performed a case study evaluating the system impact of heat-to-power conversion from smelter off-gas at a generic aluminium production facility. Results from the case study indicate that the power production potential not only depends on the energy content in the surplus heat source, but also on the conditions in the surrounding gas treatment system. The case forms a better basis for understanding the optimal integration of heat-to-power systems in the aluminium industry. The work has been published in the Energy journal.

2019 Results
Metals & Materials
Dust is a commonly encountered problem in silicon and ferroalloy smelters. Thermal processes where liquid metal comes into contact with air typically generates a form of dust, known as fume. The fume is unwanted for several reasons, one of them being the occupational health of the operators of the plant. Other issues include dust emissions to the outdoor environment, material loss (decreased yield) and various challenges with respect to ventilation and gas cleaning systems, including off gas energy recovery units. One of the processes where fuming is substantial is the casting of the alloys, a process which also holds significant potential for improved energy efficiency and recovery.
In 2019, the effect of steam/water vapor on the fume generation from silicon during casting was studied. Overheated steam has proven useful in heat exchangers for the drying of aluminium alloys and was shown to improve the efficiency of the energy recovery.
However, the casting of silicon alloys takes place at a much higher temperature (>1500°C) than the drying operations (200-250°C). Also, previous studies have shown that air humidity and moisture increased the fuming from liquid silicon which, a priori, would be detrimental for the heat recovery.
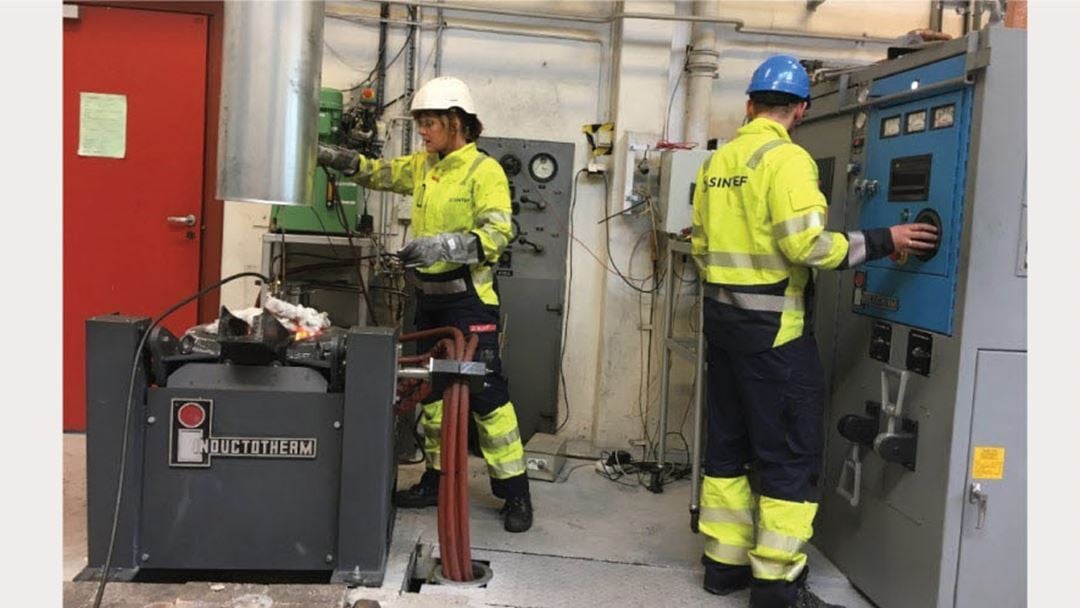
The results from this study suggest that there may be less fume formation from liquid silicon under an atmosphere with a water partial pressure over 30%, compared to the fuming in humid air and moist atmospheres (with lower water partial pressures). Hence, the use of superheated steam atmospheres in energy recovery systems for the casting processes for silicon-rich alloys cannot be ruled out based on these results and it may constitute an interesting option for further investigations. In the future, smelters will need improved dust abatement methods as well as efficient energy recovery units for the casting processes. The two aspects will, however, need to be co-developed to avoid suboptimal solutions.
Oil, Gas & Energy
Case studies in 2019 evaluated high temperature heat pumps as a means of improving energy efficiency in industry. Three different industries were studied, including an electrified offshore oil and gas platform, a nickel refinery plant and an alumina production plant. All cases demonstrate a significant potential for improvement in energy efficiency using high temperature heat pumps. For instance, results show that implementation of heat pumps for steam production at the nickel refinery plant could reduce energy consumption by approximately 75 % compared to direct electric heating. Heat pump implementation could also reduce emission of CO2-equivalents by approximately 630 tons in this case due to the emissions associated with electricity consumption.
Potential savings by implementing heat pumps for steam production at a nickel refinery plant:
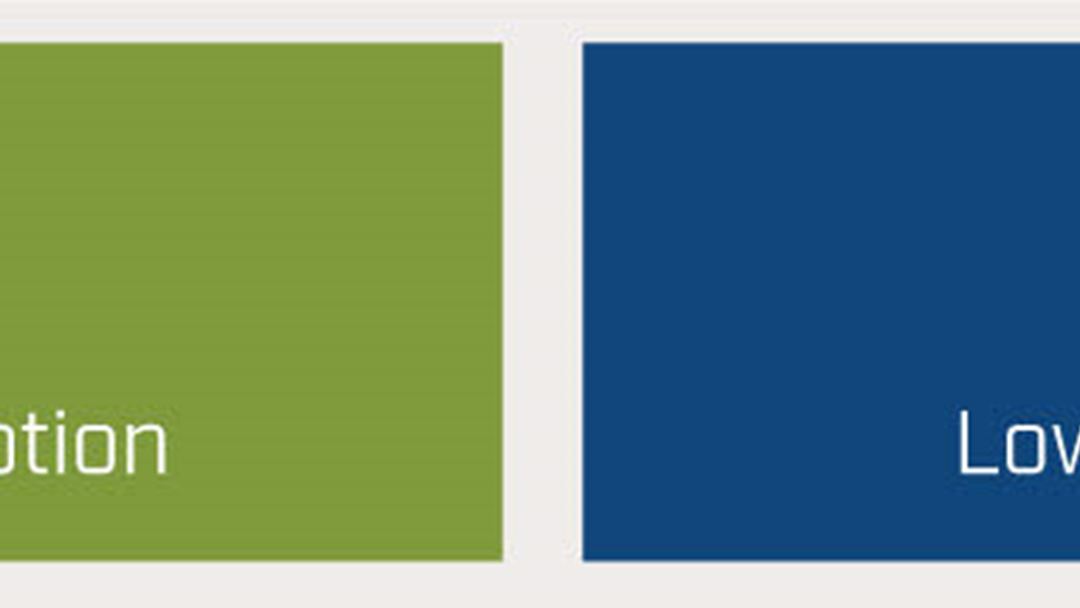
Food
The TINE dairy production site in Bergen went into production in summer 2019. The production site is based on a HighEFF case study which outlined that the heat demand of the factory can be covered with its own excess heat when using high temperature heat pumps. TINE Bergen is the first dairy in the world which does not use fossil fuel or direct electric heating. The primary energy consumption is therefore reduced by 40%. TINE was the winner of the Norwegian Heat Pump Award 2019 from "Norsk Varmepumpeforening" and the Heat Pump City of the Year Award 2019 in the DeCarbIndustry category from the European Heat Pump Association. The heat pump system was supplied by Hybrid Energi AS and supported by ENOVA.
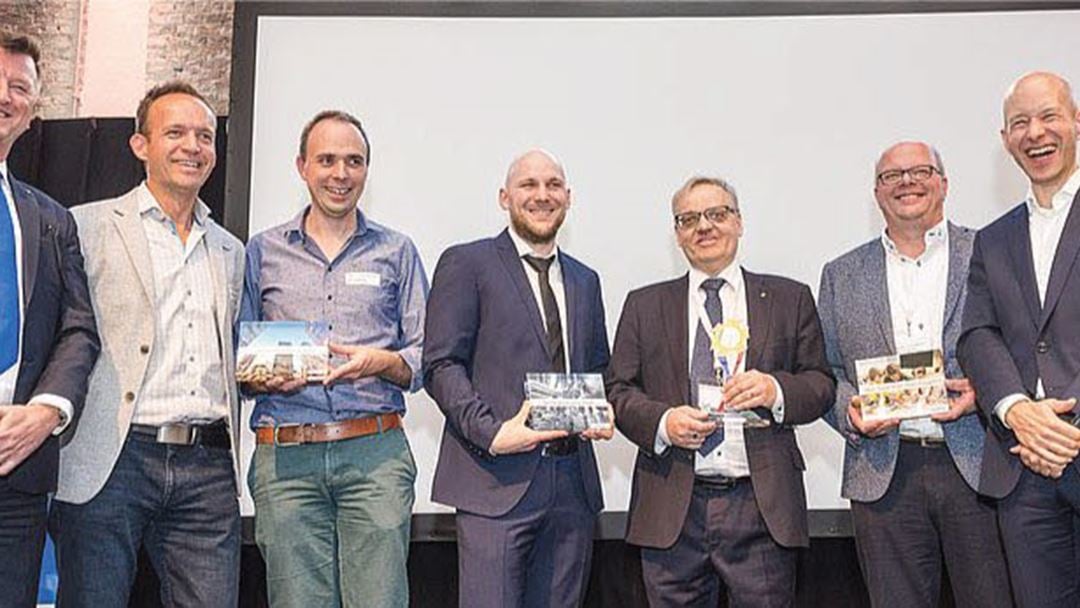
Industry Parks
Case studies within Industry parks are so far focusing on identifying promising users of low temperature industrial surplus heat. Identifying promising users forms the basis of developing successful and efficient industry parks. Based on the results of an initial screening of potential surplus heat users in 2018, three promising cases were investigated in 2019: tomato production in greenhouses, warmwater fish production in recirculating aquaculture systems, and production of insects for both food and feed. Tomato production in greenhouses can be considered the easiest to implement as it is already done both in Norway and Europe. It can potentially lead to reductions in CO2-emissions of around 75 %, but only utilizes half of the available energy due to different heat losses to the environment in summer and winter. Warmwater fish production is the second most promising case and it is already utilized in several countries. Due to lower water temperatures, heat utilization is improved compared to the greenhouse case, but it requires the development of a Norwegian or European market. Insect production is the market with the highest growth, but is currently limited to niche applications.
2018 Results
Metals, Materials and Industry Parks
The use of waste heat from aluminium electrolysis has been studied as a case in WP6.1 and 6.4, jointly. For external use, several possibilities were investigated. Vegetable/fruit production in (heated) greenhouses, fish production on land, and the drying of algae seem to be good solutions, partly due to similar existing collaborations between different industries.
For internal use, pre-heating of raw materials has been investigated. Heating of anodes has proven efficient and beneficial, both for energy efficiency and process stability. Pre-heating of the alumina feed has been investigated as well but it seems that the pre-heating temperature would need to be least 500°C, a technical challenge yet to be resolved.
Oil, Gas & Energy
A new tool for evaluation of surplus heat upgrading and heat production at industry partner sites has been developed in collaboration with WP2.1 Heat Exchangers. The tool was applied to a case study on heat production at an electrified LNG plant, which also involved evaluation of a novel and compact heat pump concept that can potentially improve the cost-efficiency of large-scale heat pump implementation. The work package has also contributed to an evaluation of heat-to-power conversion at MIP with WP3.1 Energy-to-power conversion.
Food
Two main case studies were performed in 2018; one related to chocolate production and another related to fish meal production. The chocolate production requires large amounts of electricity and gas for heating. Until recently, no alternative to gas was available, but recent development of high temperature heat pumps now enables large reductions in energy use. The gas demand can be entirely or partially removed, and electricity for direct heating reduced by about 40-80 %. Results for the fish meal case show that the suggested modifications can provide energy savings of up to 55 %, with a reduction in CO2-emissions of over 60 %.
2017 Results
Metals, Materials and Industry Parks:
Novel and conventional uses of CO rich off-gas from Mn-alloy production have been explored based on input from several consortium partners. The most relevant ideas will be evaluated from two different perspectives in future work; an industrial cluster in Mo i Rana and a stand-alone plant in Sauda. Potential for new business opportunities and technological solutions will be prioritized when selecting ideas for further study. Spin-off activities include a KPN application to EnergiX on reduced CO2 emissions in metal production, which was granted in December 2017.
Oil, Gas & Energy:
The main activity in Oil, Gas & Energy was a case study on waste heat upgrading and heat production at an electrified LNG facility. Simulation results demonstrate that state-of-the-art, high temperature heat pumps can save in the order of 30 % electricity consumption at the facility compared to a scenario where the total heat demand is covered with electric heating. The work package has also been involved in a spin-off KPN application to PETROMAKS2 on compact bottoming cycles for offshore use entitled COMPACTS2, granted in December 2017.
Food:
5 initial studies of different industry cases relevant for the food sector have been completed, with focus on novel concepts for thermal upgrading of excess heat and improved process efficiency. Applications for support funding by ENOVA have been submitted and approved for two of the cases, including a green field plant at TINE that is currently in the design phase. For this case, more than 38 % reduction in electricity demand and 40 % reduction in CO2 emissions has been determined using state-of-the-art heat pumps.