Men det har en stor ulempe – produksjonen er en av verdens største kilder til CO₂-utslipp. Omtrent 7 % av de globale utslippene kommer fra denne industrien, der kull og koks tradisjonelt brukes for å trekke ut metaller fra malm. Nå kan en ny teknologi endre dette.
Hos SINTEF forskes det på bruk av hydrogenplasma, en metode som kan erstatte fossilt karbon i metallproduksjon. Målet er å gjøre prosessen helt utslippsfri, samtidig som den opprettholder den høye kvaliteten og effektiviteten industrien er avhengig av.
Hva er hydrogenplasma?
Hydrogenplasma er en tilstand av hydrogen der gassen er ionisert, noe som betyr at hydrogenatomene har mistet sine elektroner og blitt til positivt ladede ioner. Dette skjer ved svært høye temperaturer eller ved bruk av elektriske felt. I denne tilstanden kan hydrogenplasma brukes i industrielle prosesser, som for eksempel stålproduksjon, for å redusere metalloksider uten å produsere CO₂-utslipp.
Hvis vi lykkes med hydrogenplasma, kan vi fjerne betydelige CO₂-utslipp fra metallindustrien. Dette kan være et gjennombrudd for en mer bærekraftig stålproduksjon, sier Kristine Bly, Master of science ved SINTEF.
En ny metode for en gammel utfordring
I dagens stålproduksjon fjernes oksygen fra jernmalm ved hjelp av karbon, en prosess som frigir store mengder CO₂. Hydrogenplasma-teknologien tar en annen vei. Ved å varme opp hydrogen til svært høye temperaturer, går det over i en plasmatilstand – en ekstremt reaktiv form for materie. I stedet for CO₂ dannes det kun vanndamp som biprodukt.
SINTEF har testet teknologien i HyPla-prosjektet, der forskerne har undersøkt hvordan hydrogenplasma kan brukes i produksjonen av ferromangan, en viktig legering i stålindustrien. Gjennom laboratorieforsøk og pilotprosjekter har de utviklet en metode der elektrisitet og hydrogenplasma erstatter fossile reduksjonsmidler. Foreløpige resultater viser at prosessen fungerer, men veien til storskala produksjon er fortsatt lang.
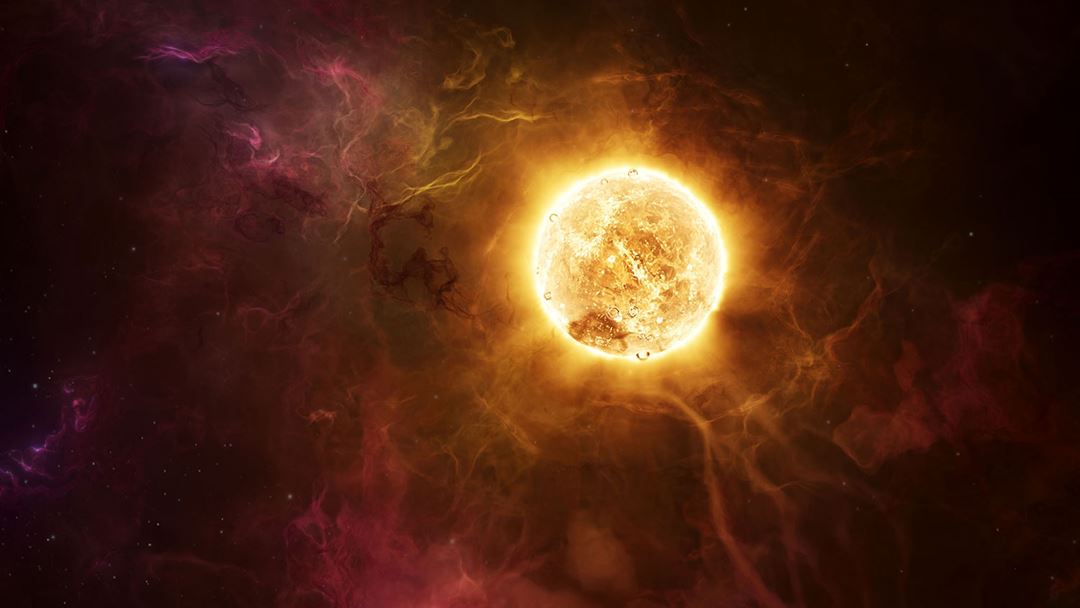
Utfordringer på veien mot industriell bruk
Selv om hydrogenplasma har vist lovende resultater, er det flere utfordringer som må løses før teknologien kan tas i bruk i stor skala. En av de største er tilgangen på grønn hydrogen. For at denne løsningen skal være bærekraftig, må hydrogenet produseres med fornybar energi. Norge har et fortrinn her med sin rene vannkraft, men det krever store investeringer for å øke produksjonen og sikre stabile leveranser.
Økonomien er også en viktig faktor. Å erstatte dagens karbonbaserte metoder krever betydelige investeringer i nye produksjonsanlegg og infrastruktur. Per i dag er det billigere å bruke fossilt karbon, noe som gjør at bedrifter kan være skeptiske til å legge om produksjonen. Samtidig ser vi en utvikling der stadig flere politiske tiltak og støtteordninger gjør det mer attraktivt å satse på utslippsfrie løsninger.
En annen utfordring er hvordan industrien må tilpasse seg denne nye teknologien. Dersom hydrogenplasma blir standarden, vil det få store konsekvenser for verdikjeden i metallindustrien. Leverandører av kull og koks vil oppleve nedgang, mens nye arbeidsplasser vil oppstå innen hydrogenproduksjon, energilagring og avansert materialhåndtering. For å sikre en smidig overgang er det avgjørende med kompetanseutvikling og tett samarbeid mellom forskning, industri og myndigheter.
En grønn mulighet for Norge
Hvis hydrogenplasma-teknologien lykkes, kan Norge ta en ledende rolle i utviklingen av bærekraftig metallproduksjon. Vi har allerede en av verdens reneste metallindustrier takket være vannkraft, men ved å ta steget videre kan vi bli en global pioner innen utslippsfri produksjon.
For at denne overgangen skal bli en realitet, må det investeres i hydrogeninfrastruktur, forskning og innovasjon. Pilotprosjektene må videreutvikles for å gjøre teknologien mer energieffektiv og økonomisk konkurransedyktig. Offentlig støtteordninger og CO₂-avgifter kan bidra til at flere selskaper tør å satse på den nye metoden.
Hydrogenplasma er fortsatt på forskningsstadiet, men utviklingen går raskt. Dersom utfordringene knyttet til energiforbruk og kostnader løses, kan denne teknologien bli en nøkkelløsning for en utslippsfri metallindustri. Spørsmålet er ikke lenger om teknologien vil bli realisert – men når.