Modern society rests on the availability of materials derived directly or indirectly from mineral resources in the earth's crust. Metals constitute a particularly important class of materials, not only as a construction material for things such as cars, planes, and buildings, but also ever more in sophisticated devices such as computers and smart phones. This has led to increased and shifting demands for metals. For example, an expanding fleet of electric cars is powered by batteries in which nickel and cobalt are key components. Globally, the nickel demand in 2030 is expected to increase by more than 50 percent over the current nickel production, just because of electric cars.
Most metals are not freely available in nature but must be extracted from the naturally occurring mineral. Nickel, cobalt, copper, and zinc are extracted in Norway by a process called electrolysis. During electrolysis an electric current is passed between two electrodes in a solution so that a metal forms at one of the electrodes. This requires large amounts of electrical energy. In Norway the production of copper, cobalt, nickel, and zinc corresponds to approximately 1 percent of the total consumption of electrical energy.
In view of the pending climate challenges it becomes imperative to reduce this energy consumption as much as possible.
The energy consumption in electrolysis can be reduced by the clever use of catalytic layers in the anode, that speed up the oxygen evolution reaction and reduces the energy consumed. Catalysts that reduce the energy consumption by as much as 15 percent are currently available in copper electrolysis. However, these rely on scarce and expensive elements which severely limit their use.
In the LEAn project NTNU and SINTEF collaborate with Glencore Nikkelverk (copper, nickel, and cobalt), Boliden Odda (zinc) and Permascand (catalysts) to reduce the energy consumption by the same 15 percent, but by developing catalytic layers relying on readily available and abundant elements.
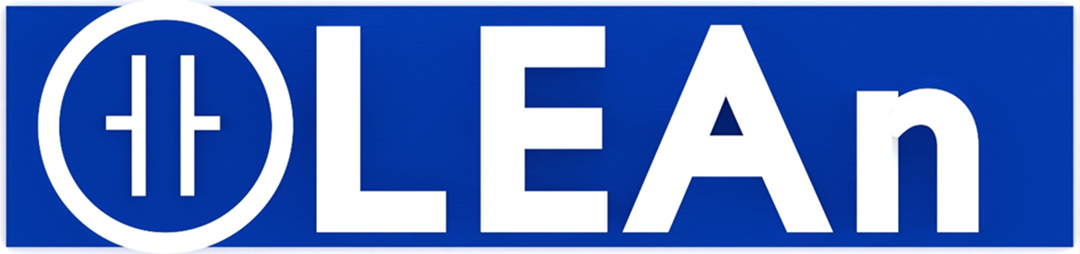
Partners
-
Norwegian University of Science and Technology (NTNU), Project Leader
- SINTEF AS, Norway
- BOLIDEN ODDA AS, Norway
- GLENCORE NIKKELVERK AS, Norway
- PERMASCAND AB, Sweden